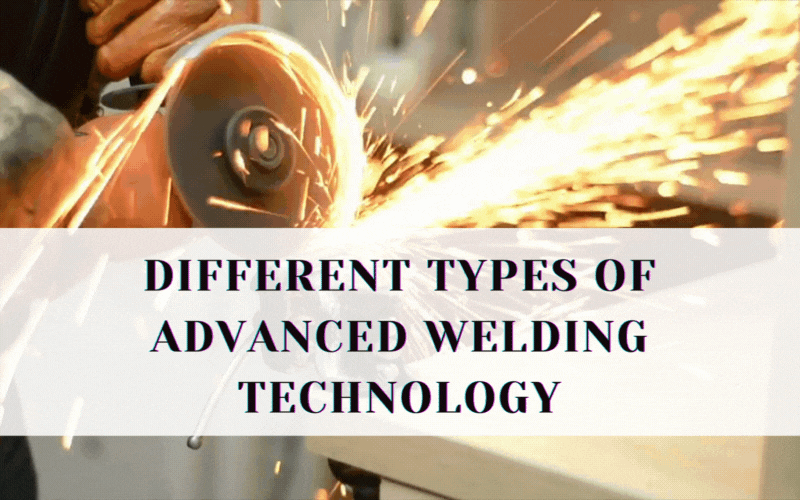
A Look at the Different Types of Advanced Welding Technology
Advanced welding technology has been on the rise in recent years, and many companies have made the switch from traditional welding methods to this newer method because of the cost savings and improved quality that it offers. If you’re interested in learning more about advanced welding technology, here are the different types used in the metals industry.
- Arc welding, TIG welding, and MIG welding
Arc welding is a type of welding that uses an electric arc to create heat. This heat is then used to weld two pieces of metal together.
TIG welding is a type of welding that uses a tungsten electrode to create heat. This heat is then used to weld two pieces of metal together.
MIG welding is a type of welding that uses a wire feeder to create heat. This heat is then used to weld two pieces of metal together.
- Plasma welding
Plasma welding uses an arc of plasma between the electrode and the base material to weld. Plasma welding is classified as a non-consumable electrode type and uses a tungsten rod for the electrode.
There are three main types of plasma welding: air plasma welding, gas tungsten arc welding, and shielded metal arc welding. Each type has its own benefits and drawbacks, so it’s important to choose the right one for your project.
- Laser welding
While perhaps not a well-known technology, laser welding has been used in various applications for decades. Its earliest use dates back to 1960 when Ford Motors Company was awarded a patent for its application in their industry.
Laser welding is a highly automated process that relies on metal deposition through a heated chamber. The primary energy source for laser welding is an infrared (IR) or UV-laser beam. These beams are converted into thermal energy via refraction as they pass through polygonal or circular mirrors before impinging on a rotating weld puddle.
This results in increased production rates and cycle times over conventional fusion welding techniques and reduces overall operating costs by minimizing losses associated with consumables such as arc electrodes.
- Robotic welding
Robot welding uses mechanized programmable tools (robots) to completely automate welding. There are a number of different types of robots that can be used in robotic welding: Cartesian, Delta, SCARA, Hexapod, Parallel and Truss robots.
The most common type is the Cartesian robot which is designed for heavy lifting and has three axes for movement. It is equipped with an arm to hold a torch and other mechanisms like clamps or grippers. These robots can weld any position by altering their angles and orientation in space.
- Flux core arc welding
Also known as dual shield welding, flux cored arc welding (FCAW) is a semi-automatic arc welding process that is similar to metal active gas (MAG) welding.
The arc is shielded by a flux, or filler metal, consisting of an inert gas such as argon and low levels of carbon dioxide. It is also commonly used to weld nickel alloys, stainless steel, and other metals that require shielding gas during welding.
- Electric spot welding
There are two types of electric spot welding: single-sided and double-sided. Single-sided spot welding is when only one electrode is used to create the arc. Double-sided spot welding is when two electrodes are used, one on each side of the workpiece.
The main advantage of spot welding over other types of welding is that it’s fast. It’s also less likely to distort the metal because less heat is applied to the area around the weld.
- Gas metal arc welding
Gas metal arc welding, more commonly known as metal active gas welding, involves a wire electrode. MIG and MAG are variants. When the wire contacts the weld pool and electric current is flowing, a bright flame forms, so that when it gets to the weld pool, it heats the pool up and it causes fusion.
There are two major different types of gas metal arc welding: short circuit and long arc. Short circuit is where we have a very high current density in a small area, which means we can penetrate up to six inches of material. Long arc gas metal arc welding does not have high current density; therefore, you’re only able to penetrate up to three-quarters or one inch in any given pass.
- Friction stir welding
There are three main types of friction stir welding: linear, circular, and orbital. Linear friction stir welding is the most common type and is used when welding two long, straight seams.
Circular friction stir welding is used for circular or cylindrical objects, such as pipes. Orbital friction stir welding is used for large objects that cannot be rotated, such as ship hulls.
Conclusion
There are many different types of advanced welding technology available to those in the welding industry. Some of the most popular include gas tungsten arc welding, plasma arc welding, and electron beam welding.
Each type has its own advantages and disadvantages, so it is important to choose the right one for your project. With so many options available, there is sure to be a type of advanced welding technology that is perfect for your needs.