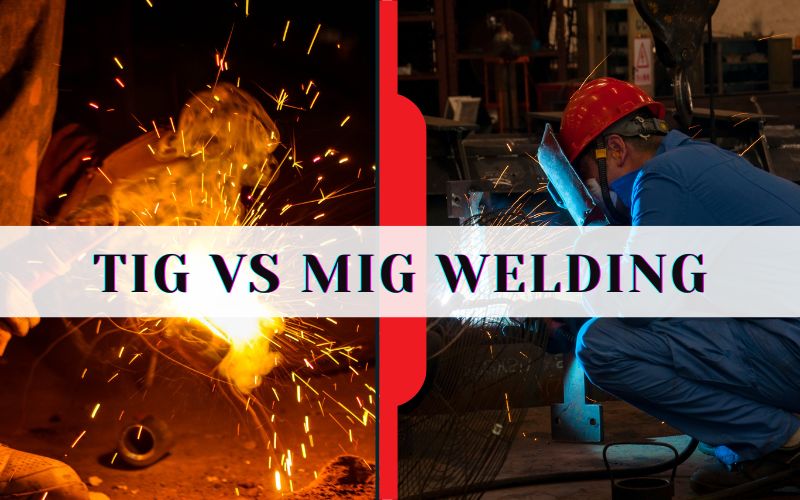
Welding 101: TIG vs MIG Welding – Which is Right for you?
If you’re just getting started with welding or looking to upgrade your existing set up, it can be hard to figure out which type of welder will best suit your needs. While both TIG and MIG welders are great options, depending on the project you’re taking on and the kind of steel you plan to work with, one might be better than the other.
This article will give you an overview of both types of welders and help you decide which one would best fit into your metalworking arsenal.
FCAW – Flux Core Arc Welding
Flux Core Arc Welding (FCAW) uses an electric current to create an arc between the electrode and the metal being welded. The arc melts and vaporizes the wire creating a pool of molten metal around the electrode tip that is drawn into, under, and up along the surface of the metal being welded.
The welder controls how much current flows through this arc by regulating either amperage or voltage while also controlling where they want to use it by moving their hand in different directions. These added control steps make FCAW welding more complex than other methods.
SMAW – Stick (or Electrode) Welding
Stick welding, often called SMAW (Shielded Metal Arc Welding), is the most common form of welding in industrial settings. The process involves covering the work with a slag shield to protect it from atmospheric contamination and burning away excess molten metal. Slag, or molten scrap that builds up on the surface of the weld, may be cut off before finishing the weld.
Stick welding is versatile because it can be used in any position and there are two techniques to choose from depending on how strong of a joint needed. A fillet weld produces stronger joints than a corner weld because it more fully penetrates both pieces being joined together than a corner weld which only attaches at two points.
GMAW – Gas Metal Arc Welding
GMAW is most commonly used for welding thick metals (thicker than .2), such as steel, stainless steel, copper, and aluminium. GMAW uses a constant flow of shielding gas to cover the weld area and protect it from oxygen while cooling the wire feeder head to keep it from heating up too much during operation. This prevents excessive penetration on thicker materials that could result in a brittle welded joint.
GMAW can be used with many different types of electrodes to provide different levels of alloying metals in the joint. Electrodes can be pure metal or they can contain some flux, which speeds up welding and provides a more stable arc.
GTAW – Gas Tungsten Arc Welding
GTAW, or Gas Tungsten Arc Welding, can be used to create a variety of welds. This type of welding method relies on an electric arc and a continuous flow of shielding gas. It’s often recommended to use when working with materials that are very difficult to penetrate and require a lot of precision in terms of shape and thickness. It also doesn’t cause thermal distortion when used with soft metals.
TIG vs MIG welding
TIG and MIG welding differ in the type of current used to create the arc. MIG welding uses gas metal arc welding, which feeds an electric current through a rod-shaped electrode, while TIG uses gas tungsten arc welding, which passes current through a wire electrode that creates an arc with a tungsten tip.
The properties of the two welds are quite different. As mentioned before, there are some instances where one type of weld may be more appropriate than another; however, it largely depends on personal preference.
Advantages of MIG welding over other welding processes
MIG welding has been used in the aerospace industry since the 1950s and was developed to weld aluminium by Union Electric Steel Company. Like MAG and GMAW, it utilizes a wire electrode for the filler metal.
The one difference between MIG welding and other processes, however, is that in order to weld a joint, only one machine with an electrode that’s kept moving must be used.
It typically produces clean lines of metallic beads on joints with little or no spatter compared to other types of arc welding. In addition, with its reduced heat input, it doesn’t leave distortions like typical arc welding processes do.
The arc length and wire feed rate must be controlled, but those values are typically pre-set in order to maintain a consistent quality of weld. In addition, it doesn’t take as much preparation to get started with MIG welding, especially in comparison to GTAW (also known as TIG welding).
Advantages of TIG welding over other welding processes
TIG welding, also known as gas metal arc welding, uses a non-consumable tungsten electrode. It’s advantageous because it has a faster travel speed and lower heat input than other welding processes.
And though there’s some give and take in terms of what can be welded, a number of alloys can be joined with the TIG process which other processes cannot. As well, TIG welding doesn’t need shielding gases or an external power source to maintain an arc while drawing on the electrode; rather, it draws its own current from the ground clamp.
In addition to these perks, larger puddle sizes make gas emissions minimal and require less cooling time before post-weld cleaning.