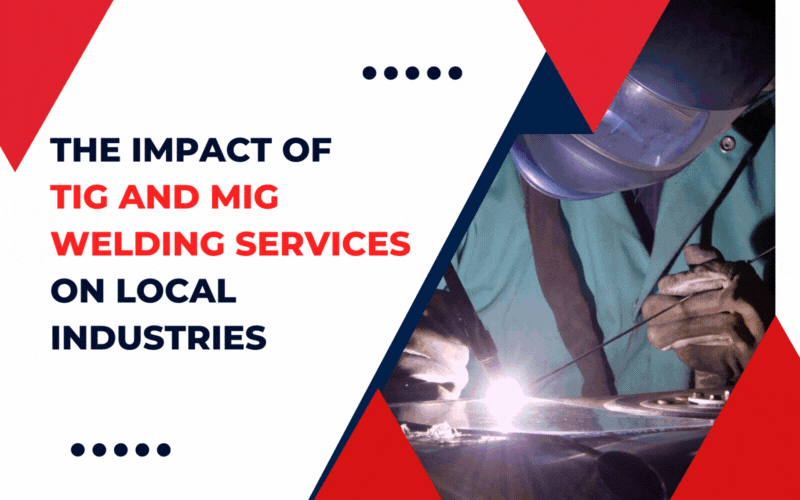
The Impact of TIG and MIG Welding Services on Local Industries
Do you ever think about how the solid structures of bridges, the stylish frames of cars, or the intricate designs of machinery come to life?
The answer to the above question is definitely TIG and MIG welding services.These two techniques are the sole power behind shaping the backbone of local industries.According to the American Welding Society, the welding industry is estimated to contribute over $50 billion to the US economy annually.
Let’s go deeper inside to find out the impact they wield and how they contribute to the growth and innovation of various sectors.
What are they actually ?
TIG welding, also known as Gas Tungsten Arc Welding (GTAW), is a manual welding process that uses a non-consumable tungsten electrode to produce the weld. The electrode is fed into the weld pool, creating a high-quality, precise weld with minimal spatter. TIG welding is best suited for thin materials, such as stainless steel and aluminium, and is ideal for welding dissimilar metals.
MIG welding, also known as Gas Metal Arc Welding (GMAW), is an automated welding process that uses a consumable wire electrode and shielding gas to produce the weld. MIG welding is best suited for large projects and high welding speeds, making it ideal for welding heavy materials, such as steel and cast iron.
Advantages
TIG welding is unparalleled in precision, making it the perfect choice for crafting with minimum deformation. Its controlled heat input and focused arc ensure the creation of precise welds.In addition, it yields clean, high-quality welds. Moreover, its versatility extends to a wide range of materials frequently used in the production of medical devices, such as stainless steel, titanium, and non-ferrous metals.
MIG welding is popular for its remarkable speed and efficiency, making it a primary choice for high-volume manufacturing applications. Its ongoing wire feed system enables quick welding, slashing labor expenses and production timelines. Moreover, it shows exceptional versatility, accommodating a wide array of metals, including steel, aluminum, and stainless steel.
Factors to Consider When Choosing the Right Welding Method
- Material Type and Thickness: TIG welding is favored for thinner materials and exotic metals, while MIG welding is appropriate for thicker materials.
- Weld Appearance: TIG welding is known for its clean and aesthetically pleasing welds, making it the preferred choice for applications where aesthetics matter.
- Welding Speed and Productivity: Speed and productivity for the project is always vital in this regard. MIG welding is the faster option, making it suitable for high-volume production whereas the other type of welding is slower but offers precision.
- Operator Skill Level: Skilled welders are always in demand for any type of welding projects. MIG welding is generally more forgiving in terms of operator technique, making it a good choice for new welders but the other one requires more skill and experience to achieve best possible outcomes.
- Cost Considerations: TIG welding is a more time-consuming procedure and requires specialised equipment, making it costlier than MIG welding. If you are concerned more about the cost of your project then MIG welding may be the more cost-effective option.
- Welding Environment: Looking into the proper welding environment, including factors like space constraints and the availability of shielding gases are quite important. MIG welding is more forgiving in less controlled environments.
- Weld Strength: The required strength of the weld must be taken into account. While both of them can produce strong welds, the choice of filler material and technique can influence the weld’s strength.
How Do TIG and MIG Welding Services Influence Local Industries?
- Boosting Productivity: With these types of welding, intricate designs and large-scale projects become achievable with relative ease. This heightened productivity translates into faster turnaround times for industries, meeting market demands efficiently.
- Ensuring Structural Integrity: In industries like construction and automotive, structural integrity is paramount. These welding services ensure that welded joints are sturdy, reducing the risk of structural failures and increasing overall safety standards.
- Promoting Innovation: The versatility of TIG and MIG welding allows for experimentation and innovation in design and manufacturing processes. Industries can explore new materials and techniques, pushing the boundaries of what’s possible.
- Reducing Costs: By simplifying production processes and reducing material wastage, these types of welding contribute to cost reduction in various industries. This cost-effectiveness enables businesses to remain competitive in the market.
Need Help Deciding?
Turn to Mobifab Today !!
Our expert welding team guarantees perfection, problem-solving, and personalized solutions for your needs. Visit us today for welding excellence!