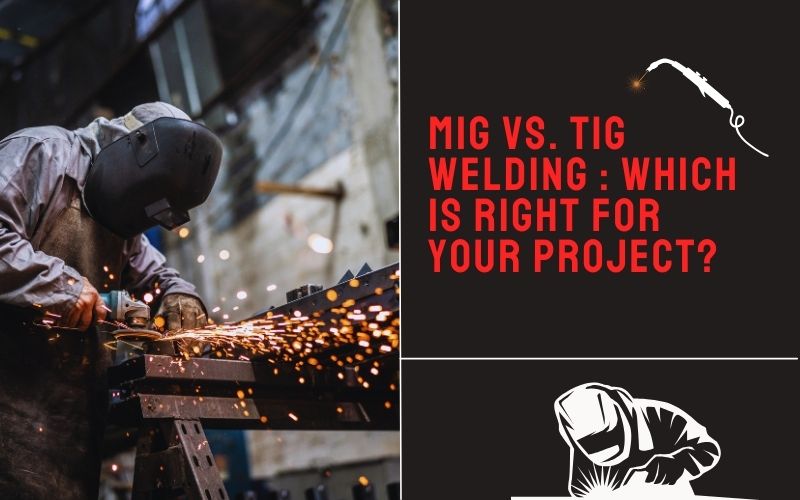
MIG Vs. TIG Welding : Which is Right for Your Project?
Ever wondered which welding method suits your project best: MIG or TIG?
MIG and TIG, two widely used welding techniques, bear resemblances in their names within the welding industry. Each method offers distinct benefits and usability. Selecting the appropriate one can result in time, cost, and labor savings, as well as positive outcomes.
Let’s explore the variances and identify the most suitable welding technique for your requirements.
Good to Know
- TIG welding, also known as Gas Tungsten Arc Welding (GTAW), is a manual welding process that uses a non-consumable tungsten electrode to produce the weld. The electrode is fed into the weld pool, creating a high-quality, precise weld with minimal spatter.
- MIG welding, also known as Gas Metal Arc Welding (GMAW), is an automated welding process that uses a consumable wire electrode and shielding gas to produce the weld.
Advantages of TIG & MIG Welding
MIG welding is well-known for its impressive speed and efficiency, making it a best choice for high-volume manufacturing needs. The continuous wire feed system allows for rapid welding, minimizing labor costs and production times.Secondly, it is highly versatile, capable of working with many metals such as steel, aluminum, and stainless steel. Its adaptable nature makes it a preferred choice in many industries. Furthermore it is user-friendly and this has made it a popular choice for those who are new learners.
TIG welding uses a non-consumable tungsten electrode and manual filler rod, providing unparalleled precision and control for delicate materials and complex joints. Welders can carefully adjust heat input and weld puddles, resulting in flawless, aesthetically-pleasing welds. This makes TIG the preferred choice in industries valuing appearance, like aerospace and food production, accommodating a wide range of materials.
Do they have any disadvantages?
Yes they do have limitations. Let’s take a glance at those as well.
TIG welding is generally sluggish than MIG welding due to the manual filler rod addition, resulting in longer production cycles and high labor costs. Additionally, it demands a higher level of skill and training, as welders must master the coordination of the electrode, filler rod, and welding torch, posing a challenge for beginners.
However, MIG welding falls short when it comes to precision, making it less suitable for complex tasks. Its weld appearance may also be less aesthetically pleasing compared to TIG welding, which could be a vital consideration for specific applications.
Let’s Compare Both
When comparing MIG and TIG welding, the first one is user-friendly, faster, and budget-friendly, ideal for thick materials and high-volume production. But the other one offers high precision and quality, suited for professionals and thin materials.
Which one is right for your project? Check out the factors
- Material Type: The type of material plays an important role in determining the most suitable welding method for your project. For thin materials like stainless steel and aluminum, TIG welding can be your suitable choice, whereas the other one is better suited for heavy materials such as steel and cast iron.
- Welding Speed: If time plays a critical factor in completing your project, MIG welding can be a more favorable option. It is a fast and efficient process. On the other hand, TIG welding is a sluggish process that is better suited for delicate and complex ones.
- Precision: If your project requires precise and excellent welding outcomes, TIG welding is the better choice. The use of a non-consumable tungsten electrode ensures a consistent arc, making it easy to beat the heat and produce consistent welds.
- Project Size: For large-scale projects MIG welding is the most preferable option. Its automated process is controlled by a wire feeder, makes the welding process quite fast and boosts productivity.
- Expenses: TIG welding is a more time-consuming procedure and requires specialized tools, making it more expensive than MIG welding. If cost is a major factor to consider, MIG welding may be the cheaper option.
By understanding the strengths of each welding method, you can choose the one that goes best with your project goals.
Ready to start your welding project?
Why Choose Mobifab’s TIG & WIG Welding Services?
- A welding team that insists on nothing less than perfection
- Welding professionals who can provide solutions to problems — based on many years of first-hand experience
- A fresh approach to every welding contract. We’ll create a customized action plan to ensure your welding requirements are delivered in full.
MobiFab: MIG or TIG Welding, Precision is Our Promise!