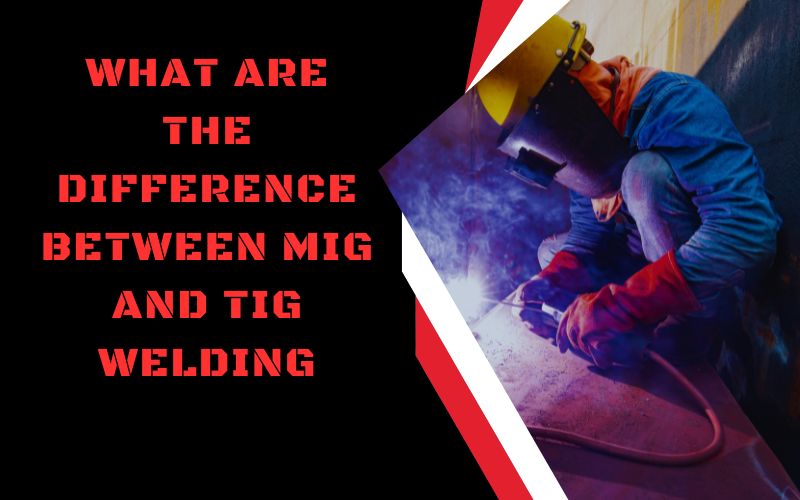
What are the Difference Between Mig and Tig Welding
Welding is an important skill that has changed the modern industrial world right from construction to automotive and so on.However deciding between TIG and MIG welding for a project is absolutely crucial to achieve success.Both these welding methods form the weld using an electric arc, though the techniques are quite different from each other. If you choose the wrong process here it could lead to waste of time, money and resources too. That’s the reason why you need to know their differences between the two.
Let us read on for the reasons.
Understanding TIG & MIG Welding
- TIG welding, also known as Gas Tungsten Arc Welding (GTAW), is a manual welding process that uses a non-consumable tungsten electrode to produce the weld. The electrode is fed into the weld pool, creating a high-quality, precise weld with minimal spatter.
- MIG welding, also known as Gas Metal Arc Welding (GMAW), is an automated welding process that uses a consumable wire electrode and shielding gas to produce the weld.
What are their advantages ?
- TIG welding is unparalleled in precision, making it the perfect choice for crafting with minimum deformation. Its controlled heat input and focused arc ensure the creation of precise welds.In addition, it yields clean, high-quality welds. Moreover, its versatility extends to a wide range of materials frequently used in the production of medical devices, such as stainless steel, titanium, and non-ferrous metals.
- MIG welding is popular for its remarkable speed and efficiency, making it a primary choice for high-volume manufacturing applications. Its ongoing wire feed system enables quick welding, slashing labor expenses and production timelines. Moreover, it shows exceptional versatility, accommodating a wide array of metals, including steel, aluminum, and stainless steel.Additionally, it also offers user-friendliness. New comers find it easy to grasp, thanks to its automatic wire feed and consistent arc.
Key Differences
1. Ease of Use
MIG welding is very user friendly and easy to learn. The continuous wire feed and simpler method make it accessible for beginners. In contrast, TIG welding demands a higher level of skill and practice. The extra challenge of handling the electrode, filler rod, and gas flow at once makes it a more challenging process.
2. Speed
When it comes to speed, MIG welding has the upper hand.It is the faster option, making it suitable for high-volume production whereas the other type of welding is slower but offers precision.The other one is slower due to its precision and the need for greater control. This slower pace can be a problem in time-sensitive situations.
3. Material Thickness
TIG welding is favored for thinner materials and exotic metals, while MIG welding is appropriate for thicker materials.
4. Quality and Appearance
TIG is a better choice when it comes to the appearance of the weld. It is cleaner with no spatter and post weld clean up is also very minimal. MIG Welding is efficient and can produce welds that need extra finishing to get a smooth appearance.
5. Versatility
TIG welding offers more versatility in the types of metals it can work with. It effectively handles a large number of materials such as steel, aluminum, copper, and others. On the other hand, MIG welding, although still adaptable, is more focused on steel and aluminum.
6. Cost
Cost is another factor to consider. TIG welding is a more time-consuming procedure and requires specialised equipment, making it costlier than MIG welding. If you are concerned more about the cost of your project then MIG welding may be the more cost-effective option.
- Operator Skill Level
Skilled welders are always in demand for any type of welding projects. MIG welding is generally more forgiving in terms of operator technique, making it a good choice for new welders but the other one requires more skill and experience to achieve best possible outcomes.
Wrapping Up,
A comprehensive approach to selecting the appropriate welding method involves careful evaluation of different factors and also consulting an experienced welding engineer.TIG and MIG welding each offer distinct benefits and limitations. Whether for delicate or bulky materials, both methods provide versatility and dependability, instilling project confidence.
Starting a Welding Project?
Choose Mobifab Today for Exceptional Results!
Why Choose Us ?
When you enlist our welding services, you get some fantastic benefits:
- A welding team that insists on nothing less than perfection
- Welding professionals who can provide solutions to problems – based on many years of first-hand experience
- A fresh approach to every welding contract. We’ll create a personalized action plan to ensure your welding requirements are delivered in full.