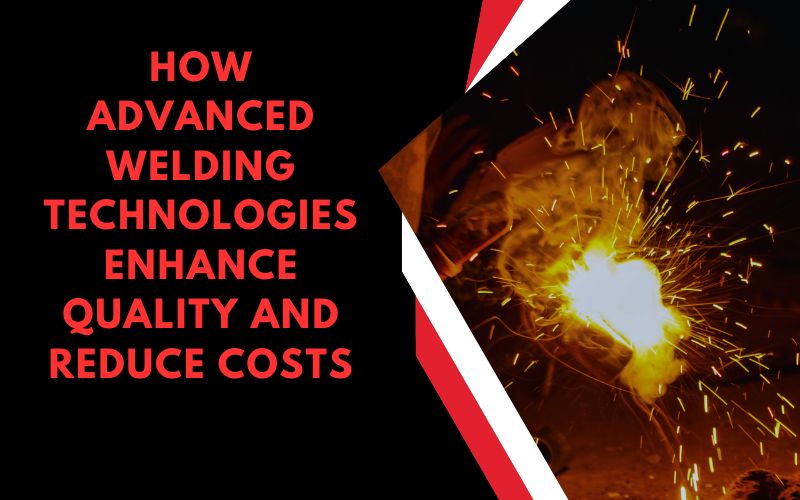
How Advanced Welding Technologies Enhance Quality and Reduce Costs
Many companies overlook the importance of the welding power source technology when assessing costs in their welding processes. Choosing the right technology can reduce expenses related to gas, wire selection, and labor, which can greatly enhance profitability.Additionally advanced welding systems and technologies can increase productivity, enhance quality, and safety, all while being easy to set up and use.
Let’s explore how these technologies transform the welding industry.
Advanced Welding Techniques
Robotic Welding
Robotic welding is a manufacturing method that employs robots to automatically handle welding and part manipulation. Typically, the only human task is to load the metal piece into the furnace.It can perform tasks with utmost precision and speed with the scope of very little human error. So the quality remains consistent which is beneficial for automotive and aerospace industries.Moreover these systems can work untiringly , increasing the rate of production. As the robotic welder can work three shifts a day , it can boost productivity and allow companies to meet deadlines.
Laser Welding
This is a process used to join together metals or thermoplastics using a laser beam to form a weld. It not only offers exceptional precision and control but also focuses on small areas resulting in minimal heat affected zones. The risk of warping or damage is very less in such cases.This type of welding is faster than the old methods.It can join materials at a rapid pace , reducing the overall production time.It leads to low labour cost with higher output.Additionally, laser welding can be applied to a variety of materials, including metals and plastics, making it versatile for different industries.
Friction Stir Welding
Friction stir welding is an innovative technique that uses friction-generated heat to join materials without melting them. This results in strong, defect-free welds, ideal for industries like aerospace and shipbuilding, where lightweight, robust components are essential. This method also reduces material waste, contributing to significant cost savings.
Enhancing Quality
These advanced technologies enhance the quality of joints, which is vital in safety-sensitive fields like automotive. A bad weld can lead to major issues. Robotic welding systems with automatic monitoring can find and correct defects instantly, ensuring dependable products. This forward-thinking method protects brand reputation and lowers expensive recalls and repairs, preventing inferior products from reaching consumers.
Reducing Costs
Cost reduction is a major benefit of these technologies. At first, the investment might appear expensive. Yet, the savings over time usually surpass the initial costs. Here’s how:
-
Labor Savings
The automation minimizes labor costs quite significantly. Robotic systems induce companies to operate with fewer welders and focus on more complicated tasks that require human expertise.This change improves how workers are assigned and can result in significant savings in the long run.
-
Material Savings
Next, these methods reduce material waste. Various techniques like laser welding and friction stir welding produce cleaner joints with less filler material. This efficiency not only checks on material costs but also contributes to a more sustainable manufacturing process.
Improved Production Efficiency
In addition, production processes are more streamlined. Faster welding speeds help companies make more products in a shorter time. This efficiency in production lets businesses better satisfy customer needs and take advantage of more market chances.
Reduced Rework and Repair Costs
Finally, good quality leads to fewer defects, which translates to lower rework and repair costs. When products meet quality standards on the first pass, companies save time and money that would otherwise be spent fixing issues. This efficiency boosts overall profitability.
Future Trends in Welding Technologies
As technology progresses, welding will experience new innovations such as AI and machine learning, which will improve settings in real time for different materials. Additive manufacturing could also introduce hybrid welding techniques that mix traditional and modern methods, improving manufacturers’ skills and increasing efficiency in the industry.
Conclusion
In summary , these technologies are revolutionizing the manufacturing industry by increasing quality and minimizing costs. Different advanced welding methods offer various benefits including improved precision, efficiency and material savings.As businesses embrace these innovations, they not only enhance their production capabilities but also position themselves for future success.
Why settle for less?
Choose Mobifab for advanced welding and cost efficiency !
Why Mobifab?
As the welding industry demands efficient solutions, our commitment to excellence resonates. They offer reliable, precise welding services to local businesses. With craftsmanship, safety, and technology, we are a proud partner in your community’s industrial success.