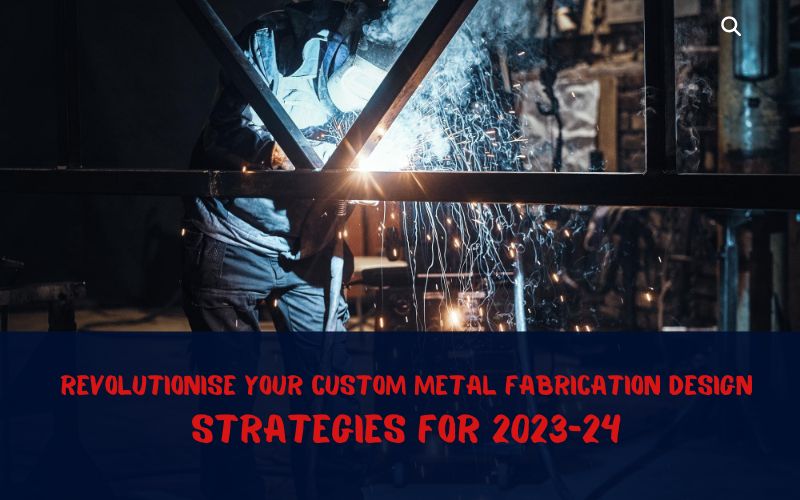
Revolutionize Your Custom Metal Fabrication Design: Strategies for 2023-24
Custom metal fabrication plays a vital role in several industries, including automotive, aerospace, construction, and many more. The demand for custom metal fabrication has been increasing and steady growth is expected in the coming years. With the advancement of technology, it is important to revolutionize your custom metal fabrication design strategies to stay ahead in this competitive market.
Latest Trends & Innovations in Metal Fabrication Design
This industry has been using quite simple processes such as cutting, welding, machining, and assembly for creating the final product. Today, the industry is highly dynamic and cyclical with its growth depending on the end-use industries. Here are some of the top trends gaining prominence in the metal fabrication industry.
- Automation
- 3D Printing
- Sustainability
- Adoption of ERP systems
- Lightweight materials
Overall, the latest trends and innovations are leading to numerous developments in this field and are driving the industry forward which helps the designers to create increasingly complex and innovative metal designs.
Key Considerations for Custom Metal Fabrication
To create a useful design, there are certain considerations you should take into account. Here are some tips to optimise your design for metal fabrication.
- Provide in depth information in your RFQ
- Eliminate irrelevant details
- Test before production
- Choose materials wisely
Advanced Techniques for Custom Metal Fabrication
Custom metal fabrication is a dynamic field and to stay in the competitive market requires a willingness to adopt new techniques and approaches. Here are some advanced techniques for revamping your design process and taking your custom metal fabrication to a higher level:
- Advanced CAD Software: Computer-aided design (CAD) software has transformed the metal fabrication industry, allowing designers to create detailed and complex 3D models quite easily.
- Embrace 3D Printing: 3D printing is an increasingly popular technique enabling designers to create complex and intricate metal parts and components with speed and accuracy.
- Incorporate New Materials: Explore the possibilities of the new materials and experiment with different combinations to create unique and innovative designs.
- Collaborate with Clients: Custom metal fabrication is all about meeting the actual needs and preferences of your clients.
- Leverage Automation: Invest in the latest automation tools and techniques to reduce waste, increase productivity, and produce better quality products.
Overcoming Common Challenges
Metal fabrication design deals with the process of creating metal products or structures by cutting, shaping, and assembling metal materials. However, like any design process, metal fabrication also faces some common challenges. Let’s check out some useful tips to overcome these challenges.
To overcome material selection, take the guidance from the experts and consider the application. To deal with design, the team needs to create detailed designs and simulations. Precision cutting and welding require specific skill sets and proper equipment. Quality control plans should include inspections, testing, and documentation. Cost management can be achieved by collaborating with suppliers and optimizing the fabrication process. Careful planning, attention to detail, and collaboration with experts can result in high-quality metal products.
How to Incorporate Feedback into Your Custom Metal Fabrication Designs
Incorporating feedback into custom metal fabrication designs requires careful analysis, revision, testing, and documentation. These steps must be followed along with fruitful communication with the client to create a final product that meets their requirements and exceeds their expectations.
Strategies for Environmentally-Friendly Practices
To design custom metal fabrication projects it’s important to consider environmentally-friendly practices to reduce waste and minimize harm to the environment. The planning may include using sustainable materials, decreasing energy usage during production, reducing water consumption, using green energy alternatives and implementing recycling and waste reduction programs. These practices not only help the environment but can also lead to cost savings and a positive reputation for the business.
Quality Control & Testing
Quality assurance stresses on providing confidence that quality requirements will be fulfilled. This component works to prevent errors through quality policies and processes. Quality control focuses on finding and correcting errors before the parts get to the customer.
Testing involves assessing the finished product to check out its performance and robustness. By implementing robust quality control and testing procedures, custom metal fabrication companies can minimize errors, improve customer satisfaction, and build a reputation for excellence in the industry.
The Future of Custom Metal Fabrication Design
Metal fabrication has long been considered one of the most stable industries in the global world of manufacturing. As the global markets shift and change in the coming years, the metal fabrication industry will greatly benefit by maintaining an attitude of versatility, flexibility and growth.
Market research indicates that the following trends such as Robotics, Automation, 3D Printing, Digitization, Cyber Security will figure prominently in the metal fabrication industry, both in the immediate future and likely for many years to come in the future.
To conclude, the metal fabrication industry is constantly evolving and organizations must keep an eye on the latest trends to stay alive in this competitive market. They need to pace up with the new technological innovations and should invest in modern tools and equipment. Moreover knowledge on the latest software will help to create unique and trendy designs which the clients might look for. By adopting these strategies and changes, these businesses can transform their operations and stay ahead of the competition in 2023-24 and beyond.