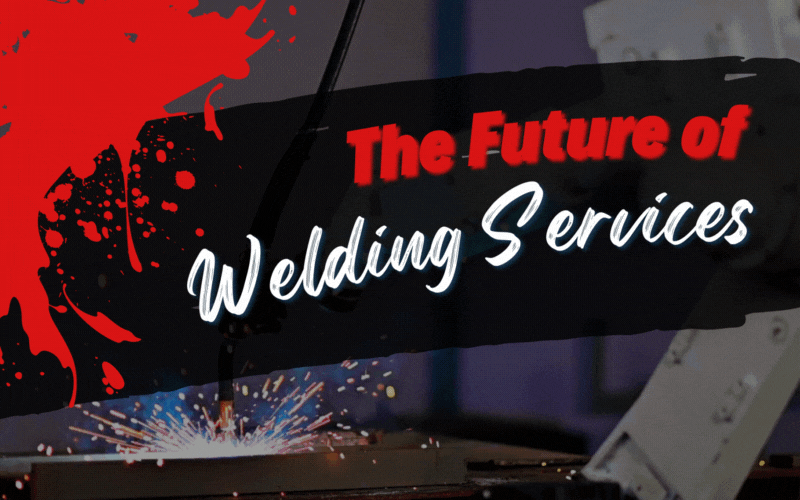
The Future of Welding Services
Welding is an essential part of various manufacturing and construction processes and has experienced significant progress from its humble beginnings.
Are you a welder,a welding contractor or part of any manufacturing / construction company?
Then you must stay up-to-date on the latest developments in this very field. So in this article let us take a closer look at the technologies and trends shaping the future of welding services.
- Automation & Robotics – One of the most innovative trends shaping the future of welding services is the adoption of automation and robotics. Traditional welding processes often require human intervention, but automation and robotics are simplifying and improving these processes.Robotic welding systems are becoming more modernized, capable of performing complex welds with precision and consistency. These systems use sensors, cameras, and advanced algorithms to analyze the workpiece and adjust welding parameters , thus offering higher productivity, improved weld quality, and reduced human error. These new trends seem highly attractive to industries for their cost effectiveness and efficiency.In addition to this robots are working alongside human welders to improve productivity.
- Advanced Materials & Techniques – New and advanced materials are used in welding as a recent trend.Manufacturers are recently developing alloys, composites and other long lasting and lightweight materials in comparison to traditional metals. Advancements in metallurgy and material science are gaining momentum for the development of new welding processes.
Another important technique is the introduction of Laser Welding which uses a highly energized laser beam to melt the metals and create a strong bond. It increases efficiency, accuracy and ability to reduce human error which in turn reduces cost and improves productivity.
- Augmented Reality Welding Helmets – Augmented Reality welding helmets have revolutionized the welding industry. These helmets provide welders with real time data such as welding parameters , work instructions , visual cues etc.The helmets are meticulously designed to enhance safety, improve accuracy and minimizing the need for reference materials.
- Safety Features – Safety is counted as the top most priority in welding and recent developments have led to new safety measures.For example , welding helmets nowadays include auto-darkening lenses to protect the welder’s eyes from the bright light emitted during the welding process.Welding machines do contain emergency stop buttons and over current protection so that accidents do not occur and workers are safeguarded.
- Personal Protective Equipment – Wearing PPE or Personal Protective Equipment is another significant trend in the welding services. These PPE’s include welding gloves, protective clothing and eye protection which protects the welders during the process.To protect the welders from harmful fumes companies are now investing in air purifying respirators which adds a feather to the latest developments taking place in the welding industry.
- Digitalization and Data Driven Welding –The future of welding services is closely tied to digitalization and data-driven approaches. Smart welding systems with sensors and connectivity capabilities can collect and interpret a large amount of data during the welding process. This data can be utilized to boost weld quality, improve productivity, and enhance overall process efficiency. Digitalization also influences remote monitoring and control of welding operations. Welding experts can remotely help and guide operators, ensuring consistency and quality across various locations. This capability is particularly helpful for industries who operate across different geographical locations or facing difficulties in getting skilled welders.
- 3D Printing & Additive Manufacturing – Additive manufacturing or commonly known as 3D printing, is revolutionizing the age old welding processes. These modern manufacturing processes are aiding in the creation of complex geometries and customised designs which in turn are opening up new possibilities for welding applications. By layering and fusing materials, 3D printing enables the production of complex metal structures with minimal material waste. This technology can act as a game changer in manufacturing industries by enabling faster prototyping, on-demand production, and economical part replacements.
- Sustainability and Environmental Conditions – In the future, welding services will prioritize sustainability and environmental concerns. Industries are becoming conscious of their carbon footprint and are using welding processes that minimize waste, energy consumption, and harmful emissions. Welding technologies are becoming much more progressive and are including cleaner alternatives like helium-based shielding gases, reducing argon consumption which is a greenhouse gas leading to global warming. Additionally, alternative power resources like renewable energy sources ensure reduced carbon emissions ensuring a reliable, sustainable energy supply for welding practices.
Conclusion
The future of welding is extremely promising, with advancements like automation, augmented reality, laser welding, 3D printing, and advanced joining techniques. These innovations lead to enhanced productivity, precision, and safety for welders.
The Welding Revolution: Advancing Industries into the Future !!