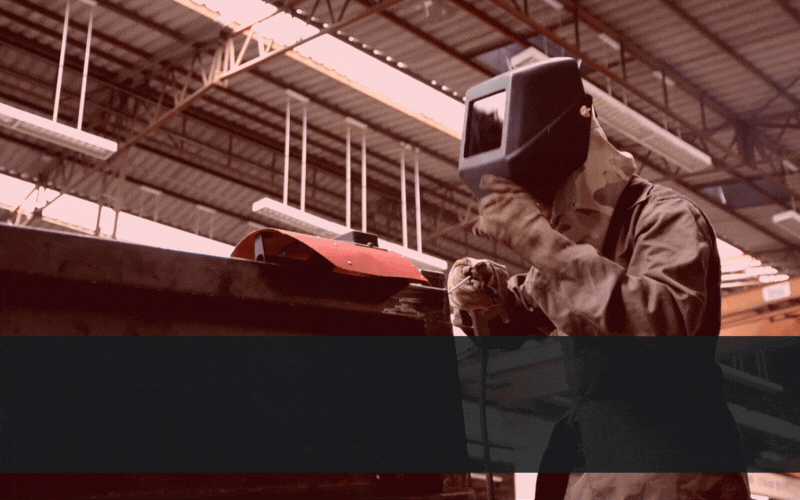
MIG vs. TIG Welding: Why MobiFab Is Your Go-To Choice
Welding serves as a comprehensive solution for metal components, playing a pivotal role in the seamless operation of our economy. Be it in the fields of automobiles, aircraft, infrastructure like bridges, or the construction of buildings, welding is the backbone that propels our economy forward.
In this article, we will look into the characteristics of MIG and TIG welding, helping you understand which one is the right choice for your specific project.
How Do We Define Welding?
Welding, a process of fabrication, involves the fusion of two or more metals through the application of heat, pressure, or a combination of both, resulting in a strong and permanent bond.
TIG & MIG Welding:
TIG welding, also known as Gas Tungsten Arc Welding (GTAW), is a manual welding process that uses a non-consumable tungsten electrode to produce the weld. The electrode is fed into the weld pool, creating a high-quality, precise weld with minimal spatter. TIG welding is best suited for thin materials, such as stainless steel and aluminium, and is ideal for welding dissimilar metals.
MIG welding, also known as Gas Metal Arc Welding (GMAW), is an automated welding process that uses a consumable wire electrode and shielding gas to produce the weld. MIG welding is best suited for large projects and high welding speeds, making it ideal for welding heavy materials, such as steel and cast iron.
Advantages of MIG Welding:
MIG welding is popular for its remarkable speed and efficiency, making it a primary choice for high-volume manufacturing applications. Its ongoing wire feed system enables quick welding, slashing labor expenses and production timelines.
Moreover, MIG welding shows exceptional versatility, accommodating a wide array of metals, including steel, aluminum, and stainless steel. Its flexibility renders it a favored method across various industries.
Additionally, MIG welding offers user-friendliness. New comers find it easy to grasp, thanks to its automatic wire feed and consistent arc. This accessibility makes it a popular choice for those new to welding.
Disadvantages of MIG Welding:
However, MIG welding falls short when it comes to precision, making it less suitable for complex tasks. Its weld appearance may also be less aesthetically pleasing compared to TIG welding, which could be a vital consideration for specific applications.
Advantages of TIG Welding:
TIG welding, on the other hand, employs a non-consumable tungsten electrode and manual addition of a filler rod to create an electric arc. Its benefits include unparalleled precision and control, making it apt for welding thin materials and complex joints. Welders can adjust meticulously heat input and weld puddles, resulting in flawless and accurate welds.
Furthermore, TIG welds are popular for their clean and visually appealing finish. This quality positions TIG welding as the preferred choice in sectors where aesthetics are supreme, such as aerospace and food production. It also exhibits exceptional flexibility, accommodating a wide range of materials, including stainless steel, aluminum, and copper.
Disadvantages of TIG Welding:
TIG welding is generally sluggish than MIG welding due to the manual filler rod addition, resulting in longer production cycles and high labor costs. Additionally, it demands a higher level of skill and training, as welders must master the coordination of the electrode, filler rod, and welding torch, posing a challenge for beginners.
Factors to Consider When Choosing the Right Welding Method
When selecting a welding method, consider the main factors. The material type determines suitability like TIG for thin materials (like stainless steel, aluminum), MIG for bulkier ones (steel, cast iron). For speed, MIG is faster; TIG is gradual but excels in accuracy and quality. Project size matters; MIG suits immense, automated tasks. Cost-wise, TIG is costlier due to its time-consuming nature and customized equipment, while MIG offers a cost-effective alternative.
Why Choose Mobifab’s TIG & WIG Welding Services?
At MobiFab, we have provided MIG and TIG welding services for just about every industry in the US. When you enlist our welding services, you get some fantastic benefits:
- A welding team that insists on nothing less than perfection
- Welding professionals who can provide solutions to problems — based on many years of first-hand experience
- A fresh approach to every welding contract. We’ll create a personalized action plan to ensure your welding requirements are delivered in full.
In summary, TIG and MIG welding each offer distinct benefits and limitations. Understanding these helps you select the suitable method for your project, ensuring desired results. Whether for delicate or bulky materials, both methods provide versatility and dependability, instilling project confidence.
MobiFab: Your Path to Precision, MIG or TIG, We’ve Got It All !