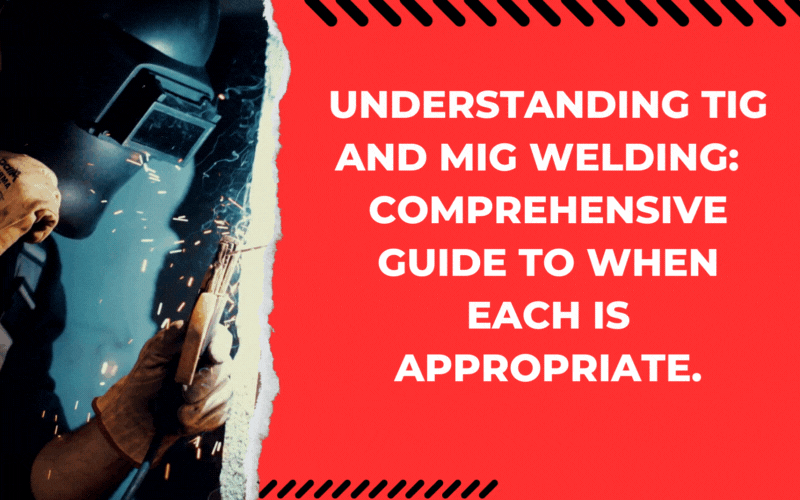
A Comprehensive Approach to When TIG and MIG Are Appropriate
Welding is a fundamental process in various industries, from automotive and aerospace to construction , repair and manufacturing. Among the many welding techniques available, TIG (Tungsten Inert Gas) and MIG (Metal Inert Gas) welding are two of the most commonly used methods. Determining the most appropriate welding methods for your project can be a daunting task, given the various options available.
What is Welding ?
Welding, a process of fabrication, involves the fusion of two or more metals through the application of heat, pressure, or a combination of both, resulting in a strong and permanent bond.
Types
TIG welding, also known as Gas Tungsten Arc Welding , is a manual welding process that uses a non-consumable tungsten electrode to produce the weld. The electrode is fed into the weld pool, creating a high-quality, precise weld with minimal spatter.
MIG welding, also known as Gas Metal Arc Welding, is an automated welding process that uses a consumable wire electrode and shielding gas to produce the weld.
Advantages of Both Welding Types
TIG welding is unparalleled in precision, making it the perfect choice for crafting with minimum deformation. Its controlled heat input and focused arc ensure the creation of precise welds.In addition, it yields clean, high-quality welds. Moreover, its versatility extends to a wide range of materials frequently used in the production of medical devices, such as stainless steel, titanium, and non-ferrous metals.
MIG welding is popular for its remarkable speed and efficiency, making it a primary choice for high-volume manufacturing applications. Its ongoing wire feed system enables quick welding, slashing labor expenses and production timelines. Moreover, it shows exceptional versatility, accommodating a wide array of metals, including steel, aluminum, and stainless steel.Additionally, it also offers user-friendliness. New comers find it easy to grasp, thanks to its automatic wire feed and consistent arc.
Choosing Between TIG and MIG Welding
The decision to use which type welding should be based on a comprehensive assessment of the specific project requirements and constraints.
Let us take a glance at the key factors ….
- Material Type and Thickness: TIG welding is favored for thinner materials and exotic metals, while MIG welding is appropriate for thicker materials.
- Weld Appearance: TIG welding is known for its clean and aesthetically pleasing welds, making it the preferred choice for applications where aesthetics matter.
- Welding Speed and Productivity: Speed and productivity for the project is always vital in this regard. MIG welding is the faster option, making it suitable for high-volume production whereas the other type of welding is slower but offers precision.
- Operator Skill Level: Skilled welders are always in demand for any type of welding projects. MIG welding is generally more forgiving in terms of operator technique, making it a good choice for new welders but the other one requires more skill and experience to achieve best possible outcomes.
- Cost Considerations: TIG welding is a more time-consuming procedure and requires specialised equipment, making it costlier than MIG welding. If you are concerned more about the cost of your project then MIG welding may be the more cost-effective option.
- Welding Environment: Looking into the proper welding environment, including factors like space constraints and the availability of shielding gases are quite important. MIG welding is more forgiving in less controlled environments.
- Weld Strength: The required strength of the weld must be taken into account. While both of them can produce strong welds, the choice of filler material and technique can influence the weld’s strength.
A Comprehensive Approach
A comprehensive approach to selecting the appropriate welding method involves careful evaluation of different factors and also consulting an experienced welding engineer. Additionally, performing test welds and prototypes can help in making a proper decision.In some cases, a combination of TIG and MIG welding, known as TIG-MIG hybrid welding, can be employed to utilize the strengths of both processes.
TIG and MIG welding each offer distinct benefits and limitations. Whether for delicate or bulky materials, both methods provide versatility and dependability, instilling project confidence.
Still Struggling For The Right Decision?
Mobifab is here to help……… Visit Us Today !!
Why Choose Us ?
When you enlist our welding services, you get some fantastic benefits:
- A welding team that insists on nothing less than perfection
- Welding professionals who can provide solutions to problems — based on many years of first-hand experience
- A fresh approach to every welding contract. We’ll create a personalized action plan to ensure your welding requirements are delivered in full.
Mobifab :Your Path To Welding Excellence !!