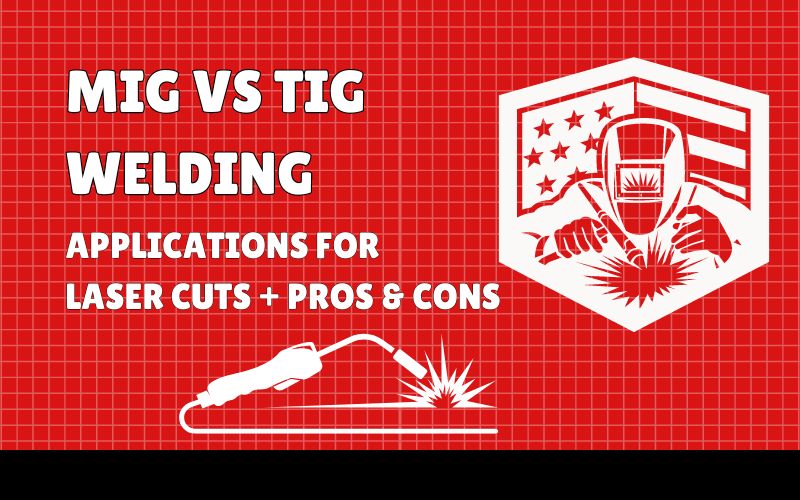
MIG vs TIG Welding: Applications for Laser Cuts + Pros & Cons
Have you ever wondered how complex metal sculptures, sturdy machinery, or even the structural framework of buildings are skillfully assembled?
Welding, the fusion of art and science, plays an important role in these projects.It is an integral and indispensable solution for metal components, driving the smooth functioning of our economy. From automobiles and aircraft to bridges and buildings, it serves as the backbone that propels our economy forward.
However, when it comes to welding laser-cut materials, which technique – MIG or TIG – takes the crown?
Let’s dive into the world of welding to expose the truth, examining their applications, advantages, and disadvantages.
TIG Welding & Its Advantages:
TIG welding, also known as Gas Tungsten Arc Welding (GTAW), is a manual welding process that uses a non-consumable tungsten electrode to produce the weld. The electrode is fed into the weld pool, creating a high-quality, precise weld with minimal spatter. It is best suited for thin materials, such as stainless steel and aluminium, and is ideal for welding dissimilar metals.
- One of the primary advantages is its efficiency and speed. The continuous wire feed allows for uninterrupted welding, significantly reducing downtime and increasing productivity.
- It also offers excellent penetration and deposition rates, resulting in strong and consistent welds.
- Additionally, it can easily handle thicker metals, making it suitable for heavy-duty laser-cut metal projects.
Applications
- Automotive Industry: From chassis to body panels,it smoothly joins laser-cut components in automobile fabrication.
- Structural Fabrication: When constructing bridges, buildings, or industrial structures, it ensures sturdy connections for laser-cut steel beams and plates.
- Shipbuilding: In marine applications, it bonds laser-cut metal parts for ship hulls, decks, and bulkheads, withstanding harsh maritime conditions.
MIG Welding & Its Advantages :
MIG welding, also known as Gas Metal Arc Welding (GMAW), is an automated welding process that uses a consumable wire electrode and shielding gas to produce the weld.It is best suited for large projects and high welding speeds, making it ideal for welding heavy materials, such as steel and cast iron.
- It excels in applications that demand utmost precision and control.
- It is particularly favored for thin, delicate metals commonly used in laser-cutting, such as stainless steel or aluminum. T
- This process allows for intricate welds with minimal heat distortion, making it suitable for projects that require aesthetic appeal and superior finish.
- Another advantage is its versatility in welding various metals, including dissimilar materials.
- It offers excellent weld quality, precise control over heat input, and minimal spatter, resulting in clean and visually appealing welds.
- It also provides better control over the welding process, making it suitable for welding joints with complex geometries.
Applications
- Aerospace Industry: It delicately joins laser-cut components in aircraft structures, ensuring lightweight yet strong assemblies.
- Artistic Fabrication: Sculptors and artists use this type of welding to fuse laser-cut metal pieces into intricate artworks, showcasing fine craftsmanship.
- Electronics Manufacturing: In electronic enclosures and components, it provides clean, precise welds without compromising the integrity of laser-cut parts.
Disadvantages
While both these welding techniques have their strengths, they also come with certain limitations.
- TIG welding is generally sluggish than MIG welding due to the manual filler rod addition, resulting in longer production cycles and high labor costs. Additionally, it demands a higher level of skill and training, as welders must master the coordination of the electrode, filler rod, and welding torch, posing a challenge for beginners.
- However, MIG welding falls short when it comes to precision, making it less suitable for complex tasks. Its weld appearance may also be less aesthetically pleasing compared to TIG welding, which could be a vital consideration for specific applications.
How to choose the right welding technique?
- Consider the thickness and type of metal, the desired finish, and the project’s complexity.
- For thicker metals and high-volume production, MIG welding offers efficiency and speed.
- For thinner, delicate metals that require precision and aesthetic appeal, TIG welding is the preferred choice.
- In some cases, a combination of both techniques may be employed. For instance, MIG welding can be used for bulk welding, while the other one can be used for complex joints or finishing touches.
Both of these welding techniques have their own benefits and limitations. Having a clear understanding of these factors allows you to choose the most suitable method for your project, ensuring the desired outcomes.
Still struggling to decide?
Let Mobifab be your guiding light.
Why Us?
- Experience perfection with our welding team.
- Get solutions from seasoned professionals.
- Personalized action plans tailored to meet your welding needs.