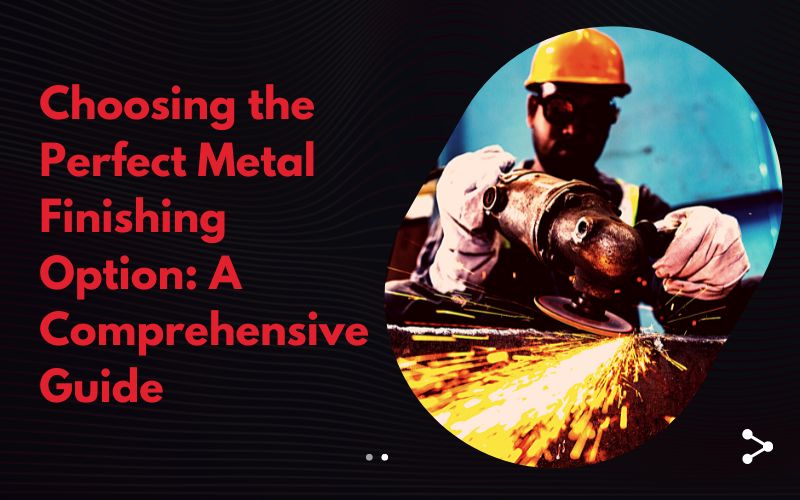
Choosing the Perfect Metal Finishing Option: A Comprehensive Guide
Unveiling Brilliance: A Journey Through Metal Finishing Excellence.
Metal finishing is a vital process that enriches the appearance, durability, and performance of metal components. It also provides environmental protection Selecting the right metal finishing option can significantly impact the final product’s quality whether it’s for industrial applications or decorative purposes. With a variety of finishing techniques available today, it’s important to understand the different options and factors to consider when making the best choice for your individual needs.
This article will walk you through the various metal finishing methods and help you make an informed decision.
Different Metal Finishing Techniques
Some common metal finishing techniques include:
a) Plating: Metal plating has the potential to enhance the durability, surface friction, corrosion resistance, and aesthetic appearance of a component.
Electroplating is a process where a thin layer of metal is deposited on the surface of a component using electrical currents. Nickel, chromium, zinc, and gold are common plating materials.
b) Anodizing: Anodizing is commonly used for aluminum and involves creating a protective oxide layer on the surface through an electrochemical process.
c) Powder Coating: Powder coating is a dry finishing process that involves applying dry paint to a surface. The dry paint, or powder, is made of finely ground particles of pigment and resin. It involves electrostatically charging a dry powder and then spraying it onto the surface to be coated.
d) Passivation: Passivation is used for stainless steel to remove contaminants from the surface and boost up its corrosion resistance. It’s a chemical process that forms a protective oxide layer.
e) Polishing and Buffing: Metal polishing reduces roughness using abrasives on machined metal. It enhances appearance and creates hygienic components.
Factors to Consider When Choosing Metal Finishing Option
a) Purpose and Application: Different finishing techniques offer varying levels of durability and aesthetics, so deciding the purpose with the appropriate finishing option is important.
b) Corrosion Resistance: Choosing a finishing technique that strengthens corrosion resistance, such as plating or anodizing, is vital for the long lastingness of the product.
c) Aesthetics: Techniques like powder coating or electroplating can provide a wide range of color options and finishes to achieve the desired look of the finished product.
d) Cost and Budget: Metal finishing costs can vary based on the technique and the intricacy of the component.
e) Environmental Impact: We need to select eco-friendly options like powder coating, which produces less waste and emits fewer volatile organic compounds (VOCs).
f) Regulatory Compliance: We need to ensure the chosen finishing option must comply with relevant standards and regulations.
g) Material Compatibility:The chosen process must be compatible with the material to achieve the desired outcome.
Let us have a sneak peak at the pros and cons of metal finishing…
Advantages
- Added chemical resistance
- Increased durability
- Increased beauty
- Higher electrical resistance
- Higher electrical conductivity
Disadvantages
- Costly for large scale projects
- Environmental Impact
- Time-Consuming
- Complexity
- Difficult Repairs
- Surface Imperfections
- Decreased Conductivity
- Limited Customization
Applications
Let’s see some examples of specific applications and the most suitable metal finishing options:
a) Automotive Parts: For automotive parts like wheels, a combination of plating and powder coating could be an outstanding selection. Electroplating the components with chrome or nickel can provide a brilliant and durable surface, while powder coating can add color options and increase corrosion resistance.
b) Electronics and Connectors: Anodizing is often chosen for aluminum electronics casings and connectors. It offers both corrosion protection and adds vibrant colors for branding purposes.
c) Architectural Elements: Powder coating provides a wide range of color choices and superb weather resistance for architectural elements like handrails.. Alternatively, anodizing can be suitable for aluminum components requiring specific colors and added protection.
d) Medical Equipment: Passivation is frequently used for medical equipment made of stainless steel. It ensures excellent corrosion resistance without changing the look or introducing potential health risks.
Conclusion
Choosing the perfect metal finishing option requires really cautious consideration of factors such as purpose, application, corrosion resistance, aesthetics, budget, environmental impact, regulatory compliance, and material compatibility. It is not only beneficial to end users, but also benefits the manufacturer if controlled carefully. Each finishing technique offers unique advantages and disadvantages, making it imperative to meet up your specific requirements with the most suitable option. By understanding the various metal finishing techniques and analyzing them for your project, you can achieve the desired results and ensure the durability and quality of your metal components.
A Gleaming Future: Power Up with Metal Finishing