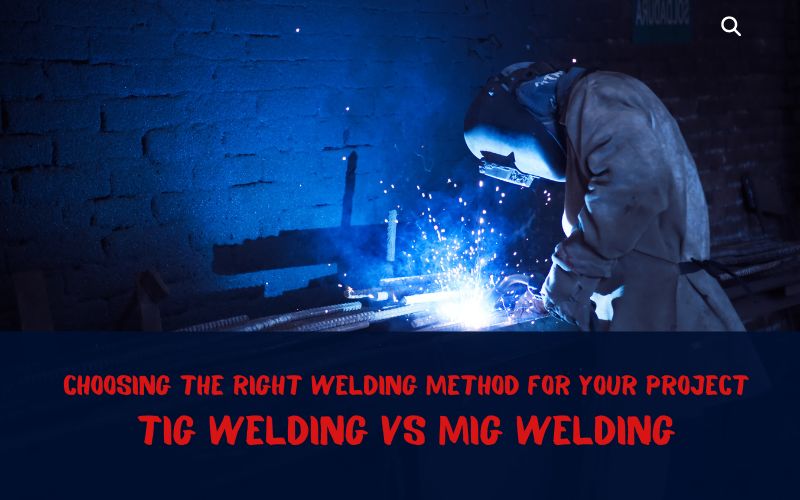
Choosing The Right Welding Method for Your Project: TIG vs MIG Welding
Introduction to TIG and MIG Welding
Welding is a fundamental process in many industries, including manufacturing, construction, and repair. Determining the most appropriate welding methods for your project can be a daunting task, given the various options available. TIG and MIG welding are two of the most commonly used welding methods, each with their unique advantages and disadvantages.
Comparing TIG and MIG Welding Techniques and Advantages
TIG welding, also known as Gas Tungsten Arc Welding (GTAW), is a manual welding process that uses a non-consumable tungsten electrode to produce the weld. The electrode is fed into the weld pool, The TIG welding technique, a form of arc welding where the electrode is fed into the weld pool, is a versatile, precise, and highly advanced method of joining a variety of metal types. TIG welding is best adapted for thin materials, such as stainless steel and aluminium, and is ideal for welding dissimilar metals. The TIG welding process is a highly sophisticated, precise, and versatile arc welding method that joins almost all metals.
MIG welding, also known as Gas Metal Arc Welding (GMAW), is an automated welding process that uses a consumable wire electrode and shielding gas to produce the weld. In fact, MIG stands for metal inert gas. MIG welding is most appropriate for large projects and high welding speeds, making it optimal for welding heavy materials, such as steel and cast iron.
TIG Welding: Ideal for Thin Materials and Precise Welds
TIG welding is a sluggish operation, which can make it time-consuming for large projects. However this welding method is renowned for its precision and high-quality welds produced with TIG welding make it ideal for delicate and intricate projects, such as welding thin metal sheets or delicate welding joints.
The non-consumable tungsten electrode used in TIG welding provides a stable arc, easing it to control the heat and produce consistent welds. The electrode is also less likely to contaminate the weld, lowering the potential risk of porosity and ensuring a high-quality finished product.
MIG Welding: Ideal for Large Projects and High Welding Speeds
MIG welding is a speedy and productive process, making it ideal for large projects that require a high volume of welding. The automated process of MIG welding can also be controlled with a wire feeder, boosting the speed and uniformity of the welds.
The consumable wire electrode used in MIG welding provides a high deposition rate, allowing for faster welding speeds and boosting productivity. MIG welding is also less demanding physically, as the welder does not need to give manual effort to put the electrode into the weld pool.
Factors to Consider When Choosing the Right Welding Method
When choosing the right welding method for your project, it is important to consider the following factors:
- Material Type: The type of material you are welding will play a vital role in figuring out which welding method is best adapted for your project. TIG welding is most preferable for thin materials, such as stainless steel and aluminium, while MIG welding is best suited for heavy materials such as steel and cast iron.
- Welding Speed: If time is of the essence for your project completion, MIG welding is the more suitable alternative to consider as it is a fast and efficient process. TIG welding, on the other hand, is a sluggish process that is better suited for delicate and intricate projects.
- Precision: If your project requires accurate and exceptional welding results, TIG welding is the better option. The non-consumable tungsten electrode used in TIG welding provides a consistent arc, making it easier to control the heat and produce consistent welds.
- Project Size: If you are working on a large project that requires a high volume of welding, MIG welding is the most preferable option. The automated process of MIG welding can be controlled with a wire feeder, speeding up the process and enhancing its productivity for big scale projects.
- Expenses: TIG welding is a more time-consuming procedure and requires specialized equipment, making it costlier than MIG welding. If you are concerned more about the cost of your project then MIG welding may be the more cost-effective option.
Conclusion
Choosing the appropriate welding technique for your project plays a vital role in the success of the project and the quality of the final product. TIG welding is best suited for thin materials and specific welds, while MIG welding is ideal for large projects and high welding speeds. Taking the material type into consideration, welding speed, precision, project volume, and expense, you can determine the optimal welding method for your project.
In conclusion, both TIG and MIG welding have their distinct pros and cons. To differentiate between the two methods, you can determine the right welding method for your project and ensure that you achieve the desired outcome. Whether you are welding sensitive and intricate projects or large, heavy materials, TIG and MIG welding offer the versatility and dependability that you need to complete your project with confidence.