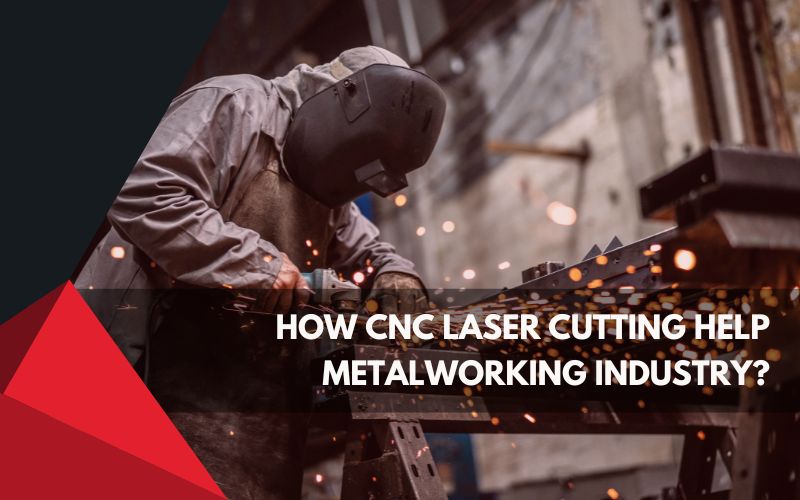
How CNC Laser Cutting help Metalworking Industry
When we speak about metalworking, the terms precision and efficiency are of utmost importance. Manufacturers constantly work hard to speed up their processes and deliver high-quality products on time. One technology that has played a significant role in achieving these goals is CNC laser cutting. The implementation of laser cutting machines has greatly advanced sheet metal processing technology and revolutionized the way metals are to be fabricated and processed. This is due to its accuracy, versatility and speed. CNC laser cutting brings numerous benefits to manufacturers and customers.
CNC, or Computer Numerical Control, involves the automated control of machine tools using computer programming. Laser cutting, on the other hand, utilizes a high-powered laser beam to cut through materials to get exceptional precision while cutting various materials. When these two technologies combine, they create a great combination that provides unparalleled benefits.
In this article, we will explore how CNC laser cutting has helped shape the metalworking industry by looking into its key benefits and applications.
Unparalleled Precision – Precision is the foundation of metalworking, and CNC laser cutting excels in this regard. By employing computer-controlled systems like CAD & CAM , CNC laser cutters are capable of executing complex designs and achieving precise cuts consistently. The laser beam’s high energy density allows for accurate cuts, enabling manufacturers to create intricate and complex geometries that were previously difficult to achieve with age-old cutting methods. This level of precision increases the product quality and diminishes the need for additional finishing procedures.
Versatility in Material Processing – The versatility of CNC laser cutting extends beyond metal processing in terms of the materials it can process.While well-known for its mastery in metal cutting, laser technology also excels in handling non-metallic substances such as wood, acrylic, and plastics. This wide scope of compatibility presents manufacturers with the opportunity to diversify their product offerings and cater to a wide range of industries.Automotive parts, aerospace components, signage, or decorative pieces, CNC laser cutting finds widespread application across different sectors, placing itself as a valuable property for the metalworking industry.
Enhanced Efficiency and Speed – Speed and efficiency are vital factors in any manufacturing process, and CNC laser cutting outperforms in both areas. The automation provided by CNC systems rejects the need for manual adjustments and reduces setup time. Once programmed using dedicated computer softwares, the CNC laser cutting machine can consistently repeat the same design with minimum operator intervention, resulting in faster productions. The laser’s rapid cutting speed further adds to the efficiency, allowing manufacturers to meet demanding deadlines and increase industrial productivity.
Cost Savings – CNC laser cutting can be cost-effective to metalworking businesses. Firstly, the precision of laser cutting decreases material waste by maximizing the use of raw materials. The narrow kerf width of the laser beam reduces the amount of material lost during the cutting process, ultimately lowering production costs. Moreover, CNC laser cutting eliminates the need for multiple tools and setups,simplifying the manufacturing process and reducing manual labor requirements. With fewer manual interventions and secondary operations, such as deburring or finishing, businesses can save on labor costs while they can still maintain high quality output.
Improved Safety Measures – Safety is paramount in any industrial setting, and CNC laser cutting machines include various safety features to protect operators. The automated methods reduce direct human interaction with the cutting operation, reducing the risk of potential accidents and injuries. Furthermore, laser cutting machines are typically done in an enclosed area, preventing the spreading of fumes and hazardous emissions into the workspace. These safety measures ensure a protective working environment and encourage the overall well-being of the workforce.
Apart from the above factors we may add that laser cutting is also highly repeatable, with no damage to the surface of the material. It can be easily programmed to process any design, making it an economical choice for cutting large metal sheets without the need for molds. The laser cutting process is also highly adaptable, as it exerts no cutting force and generates no tool wear. This makes it an appropriate process for cutting a wide range of materials. One of the key benefits of the laser cutting process is that the mechanical part of the laser cutter never comes into contact with the workpiece. Hence there is no risk involved in getting scratches or other surface damage.
Conclusion
CNC laser cutting has undoubtedly reinvented the metalworking industry.offering unprecedented levels of precision, versatility, efficiency, and safety. The assets that it provides, such as precision cutting, material versatility, enhanced efficiency, cost savings, and improved safety measures, have catapulted the metalworking industry into new domains of productivity . As technology continues to evolve, CNC laser cutting will undoubtedly continue to play a decisive role in shaping the future trends of the metalworking industry.