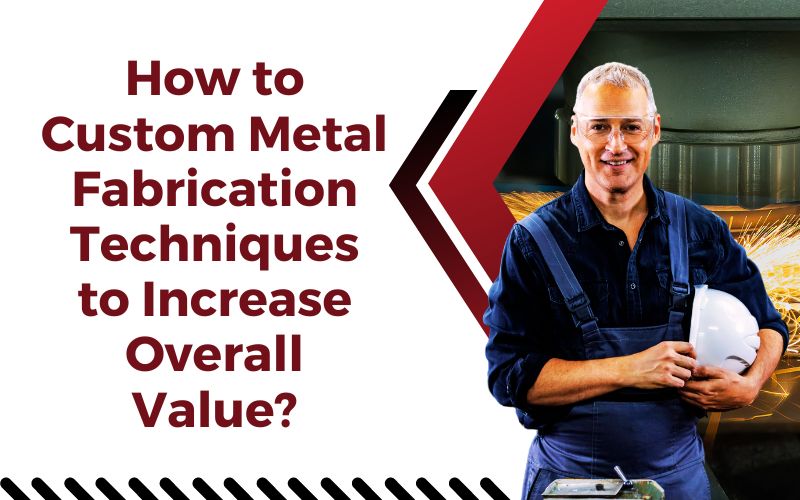
How to Custom Metal Fabrication Techniques to Increase Overall Value?
Custom metal fabrication is an essential process in various industries and value is what sets apart a regular metal fabrication project from a custom-made one.From start to finish, this process aims to create durable and high-quality results that offer long-term value.The process starts with careful research to determine the best materials and methods for cost-effective production of each unique design.Then only businesses can maximize the overall value of their metal products.
How Can Custom Metal Fabrication Techniques Boost Overall Value?
Let’s check out the answer to this question…
- Enhancing Design Flexibility – The main ways to increase the value of this fabrication is through design optimization. It involves careful consideration of the intended use and functionality of the product and designing it accordingly. By working closely with engineers and designers, businesses can create metal components that are more efficient, durable, and have a pleasing appearance.
- Metal Fabrication & Shaping – Before cutting metal, a fabricator must choose the right method based on metal type and thickness. Laser cutting is great for delicate or heavy steel, but not for composite metals. Plasma machines with CNC offer precision for complex shapes. Sawing suits structural steel, while plate shears are best for simple shapes. Forming methods include bending, rolling, and punching, with various machinery options available for each task.
- Tailored Welding & Integration – Custom welding and assembly techniques ensure metal fabrications meet industry standards. Fabricators with certified welders and a quality control program are more likely to meet these standards.Before choosing a fabricator, ask for documentation of welder certifications, adherence to industry standards like CWB, ASME, and AWS, and evidence of thorough testing and documentation in their QC program.Efficient shipping of complete or large subassemblies can reduce project timelines and costs.
- Material Selection – Selecting the appropriate materials is necessary for achieving high-quality custom metal fabrication. The selection process should consider factors such as strength, corrosion resistance, weight, and cost. Using advanced materials, such as alloys or composites, can offer improved performance and durability.Moreover, businesses should explore sustainable and eco-friendly material options to align with growing environmental concerns. By using recycled or recyclable materials, companies can enhance their reputation and appeal to environmentally conscious customers.
- Advanced Techniques – Embracing advanced manufacturing technologies is another effective way to increase the overall value of this technique. Techniques such as computer numerical control (CNC) machining, laser cutting, and 3D printing allow for precise and intricate designs, reducing production time and costs without compromising with the high quality of the products.Automation and robotics can also improve efficiency and consistency in fabrication processes. By using these technologies, businesses can achieve higher productivity, reduce errors, and enhance the repeatability of their products.
- Quality Assurance & Inspection – To ensure the value and integrity of these projects, implementing proper quality assurance and inspection processes is absolutely necessary. This involves conducting detailed inspections at various stages of production to identify and rectify any defects or deviations from design specifications. By following strict quality control standards, businesses can deliver products that meet or exceed customer expectations, enhancing their reputation and customer satisfaction.
- Leveraging Sustainable Practices – As sustainability becomes an increasingly important consideration for consumers and businesses alike, custom metal fabrication can be used to reduce environmental impact. By improving material usage, reducing waste, and implementing energy-efficient manufacturing processes, businesses can minimize their carbon footprint and enhance their eco-friendly credentials. Sustainable practices not only connect with environmentally conscious consumers but also contribute to long-term cost savings and brand reputation, thus increasing overall value.
- Customization and Personalization – Custom metal fabrication inherently offers opportunities for customization and personalization. By understanding and accommodating unique customer requirements, businesses can add value to their products. This may involve incorporating specific designs, finishes, or branding elements into the fabrication process.
- Enhancing Value through Finishing – Ensuring durability will provide a significant return on investment. The finishing methods, including metal bead blasting for surface preparation, controlled paint booths for custom painting, hot-dip galvanizing, and metal powder coating, protect structures like oil and gas tanks and grain silos from harsh outdoor conditions, preserving their valuable contents.
Embracing innovation and staying up-to-date with the latest fabrication trends will be crucial in maximizing the value and success of custom metal fabrication projects in the years to come.
Seeking Exceptional Custom Metal Fabrication Services in South Carolina?
Crafting Excellence, Molding Metals: Select Mobifab – Your Ultimate Metal Fabrication Companion !