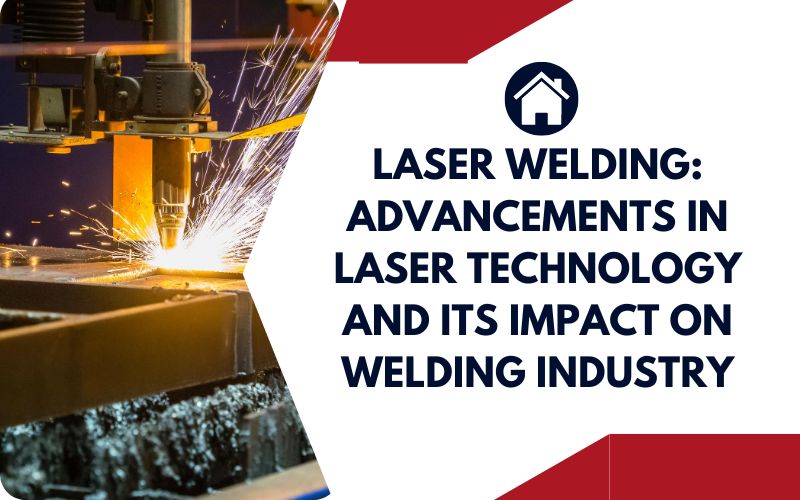
Laser Welding: Advancements in Laser Technology and Its Impact on Welding Industry
Laser welding has emerged as a promising technology in recent years, offering numerous benefits over traditional welding methods. Among novel techniques, laser welding is considered as an adaptable and rapidly evolving method, finding innumerable applications in engineering industries such as automotive, aerospace, electronics and medical equipment due to its high precision, speed, and efficiency.. It is capable of welding narrow and impassable joints precisely, which can be operated under computer control.. This article will explore the advancements in laser technology and their impact on the welding industry.
Understanding the Basics of Laser Welding Technology
Laser welding is a procedure in which metals or thermoplastics are connected to create a weld using a laser gleam. Due to the concentrated heat source, laser welding can be performed at high welding velocities in metres per minute in thin materials.
Laser welding consists of an extremely high power density laser beam; the beam is powerful enough when it is focused on the metal to vaporise a hole through the metal and the keyhole thus formed. As the beam passes through the joint, the metal starts to melt, creating a melt pool that flows into the rear of the keyhole, the molten metal solidifies and forms a weld.
The two types of laser welding are:
- Heat Conduction Welding.
- Deep Penetration Welding (Keyhole).
Heat conduction welding uses low power density, which is less than 106 W/cm2, heating the workpiece to a temperature above the melting temperature without vaporising whereas Keyhole welding uses a high power density of 105 – 106 W/cm2, heating the workpiece above the evaporating temperature and creating a keyhole due to the flowing metal vapour’s ablation pressure.
Advantages of Laser Welding: The Benefits of Using Laser Technology for Welding
Metal fabricators utilise a range of welding techniques to connect metal parts together. The selection of a particular welding method depends on its benefits and limitations, which determine its appropriateness for various applications.One of the most popular welding methods used in today’s metal fabrication projects is laser welding. As the name suggests, this welding process involves fusing metal parts together through laser technology.
Below are some of the most significant advantages of laser welding……
High Precision – In welding applications where details matter, laser welding is a clear winner. It is a tightly controlled welding method that can deliver a high level of precision that may not be possible with traditional welding technologies. This makes it possible to perform the most intricate welding tasks without compromising the weld joint quality.
High Strength – As a type of fusion welding, laser welding helps to create high-strength weld joints that ensure the safety and stability of metal products. The high heat of the laser beam helps to effectively heat metal parts to their melting points, allowing them to form a strong bond as they cool.
High Efficiency – Laser welding allows for efficient production of weld joints because the laser beam used in welding applications is highly concentrated. Almost all of the heat energy produced by the laser is used to melt and join metal parts together, forming high-strength bonds in the process.
High Production Speed – When carried out as an automated process, laser welding can be optimised to produce high-quality welds at a fast and consistent rate. This makes it an excellent choice for projects that require a high production volume.
Minimal Thermal Distortion – Because it’s a low-heat welding process, laser welding minimises heat-affected zones, reducing the need for re-working. This not only helps to minimise material deformity but also lowers production costs.
Increased Flexibility – Laser welding not only allows metal fabricators to join different types and thicknesses of similar and dissimilar metal parts together but also allows them to perform welding tasks in otherwise inaccessible areas.
Reduced Labour Costs – Laser welding can be automated, reducing the need for manual labour in the welding process. This results in reduced labour costs and improved worker safety.
Environmental Benefits – Laser welding produces minimal fumes and emissions, making it a more environmentally friendly option than traditional welding methods. It also requires less energy than other welding methods, reducing the overall carbon footprint of the welding process.
Recent Innovations in Laser Welding Technology: A Look at the Latest Developments
Laser welding has been around for several decades, and over the years, the technology has continued to evolve and improve. Recent innovations in laser welding technology have enabled manufacturers to produce higher-quality welds at faster speeds and with greater efficiency than ever before.
Let’s have a look at some of the latest developments in laser welding technology…..
- Fibre Laser Technology – Fibre lasers are solid state lasers in which an optical fibre doped with low levels of a rare earth element is the lasing medium. Fibre laser technology has transformed the laser welding industry by offering higher beam quality, better energy efficiency, and faster welding speeds.
- Hybrid Laser Welding – Hybrid welding technology can be defined as the combination of a laser heat source with a secondary welding source, typically an electric arc. The hybrid welding processes have some advantages over arc welding and laser welding like high welding speeds, reduction of edge preparation accuracy, control of metallurgical variables through the addition of filler wire and higher electrical efficiency.
- Remote Laser Welding – Recent advancements in scanner optical configurations, scanner controls, and real-time interfaces to optical sensors have significantly expanded the application of remote laser welding.
- Multi-beam Laser Welding – It is a type of laser welding process where multiple laser beams are used simultaneously to weld a single joint. This technique is commonly used in industries such as automotive, aerospace, and electronics, where high-speed and high-precision welding is required.
- High-Speed Laser Welding – High-speed laser welding is a new technology that enables manufacturers to weld at speeds of up to 100 metres per minute. This approach offers important advantages for high-volume production, as well as for welding thin materials, such as sheet metal.
Laser Welding Applications: Exploring the Wide Range of Industries and Uses
Laser welding is a highly precise and efficient welding method that uses a focused beam of laser light to melt and join two materials. This technique is used in a wide range of industries and applications, from automotive and aerospace to medical and electronics.
1.Automotive Industry
The automotive industry is one of the biggest users of laser welding technology. This is due to the high accuracy and speed of laser welding, which allows manufacturers to produce excellent-quality automotive components in large quantities.
2.Aerospace Industry
The aerospace industry requires topnotch-quality welding to produce reliable and safe parts. Laser welding has found its application in the aerospace industry due to its ability to weld high-strength alloys and lightweight materials. The precision and speed when welding with lasers make it an ideal process for welding thin materials used in the production of aircraft components, such as control surfaces, wings, and fuel tanks.
3.Medical Industry
The medical industry has found several applications for laser welding. A Laser welding machine is used to manufacture medical implants, instruments, and devices that require high precision and accuracy.
4.Electronics Industry
The electronics industry has also found various applications for using a handheld laser welder. Laser welding is used for welding electronic components such as sensors, connectors, and batteries.
5.Jewellery Industry
The appearance of a handheld laser welding machine has revolutionised the jewellery industry by providing a more precise, accurate, and efficient welding process. The precise welding allows the manufacturer to create intricate designs and improve the quality of the final product.
Laser Welding vs. Traditional Welding
The main advantage of laser welding over conventional techniques is that it can be used in precision applications where accuracy is paramount. This makes it perfect for situations where complex parts must be welded together with pinpoint accuracies, such as in medical devices or aerospace components. Additionally, because the weld area is very small, there’s less heat distortion which helps reduce post-weld processing time. Furthermore, since no filler material or heat shield is required, there’s less chance of contaminants entering the weld joint and causing weak spots or cracks. Finally, because lasers don’t require direct contact with the workpiece during welding, they’re better suited for working on delicate components that would otherwise be damaged by physical contact with traditional tools.
Laser Welding Safety: Tips and Best Practices for Safe Laser Welding
With laser welding, human intervention is limited. The welding robot seams the parts on its own. That leaves many workers asking these questions. Is laser welding safe? The answer is yes. But does laser welding still present risks to humans? The answer to that question is also yes. Here are some problems that could come up while working around laser welding equipment.
While it is safe, precautions need to be taken due to the highly-concentrated heat source that can cause fire and injury. The process also produces welding fumes that can be harmful to humans, especially when welding galvanised parts. Light-tight enclosures are necessary to prevent harmful light from escaping the weld area and causing damage to the plant and workers.
The Future of Laser Welding: Predictions and Projections for Laser Welding Technology
Looking ahead, the future of laser welding appears to be bright. Laser welding has obtained great development from the research and engineering application of procedure processing, welding procedure treatment, and welding defect resolution. With the constant breakthrough and development of brand-new laser devices, it is foreseeable that soon, the application fields of laser welding innovation will continue to be applied to more material processing terminal fields, helping the commercial upgrading of manufacturing. Here are some predictions and projections for the technology:
- Increased adoption
- Improved automation
- Advances in Technology
- Greater use of hybrid welding
To conclude , laser welding has transformed the welding industry with its accurate, efficient and fast outcomes. Advancements in laser technology have enhanced its capabilities, making it a preferred choice for several applications. The advantages of laser welding, including reduced heat input and enhanced productivity, have made it essential in many manufacturing industries. In future as technology advances, it will improve its accuracy, efficiency, and versatility, cementing its position as a game-changing technology with a growing impact on the welding industry.