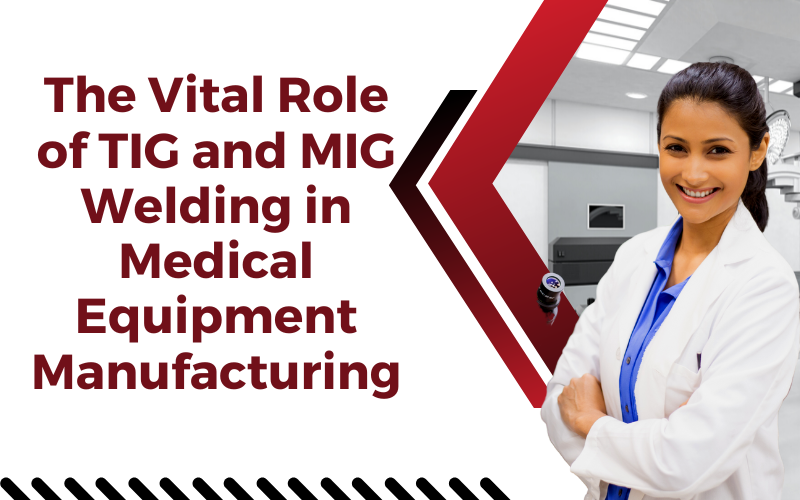
The Vital Role of TIG and MIG Welding in Medical Equipment Manufacturing
In recent years we have seen the first hand growth of medical device manufacturing. Welding is an essential part of medical equipment manufacturing and it plays a pivotal role in the healthcare industry. The manufacturing of medical devices require reliability , precision and following strict quality standards. TIG (Tungsten Inert Gas) and MIG (Metal Inert Gas) welding plays a vital role in ensuring high quality production of medical equipment. Medical device welding is required to produce many life-saving medical devices, including surgical instruments, implants, and diagnostic equipment.
This article explores the significance of TIG and MIG welding in the manufacturing process of medical equipment, focussing on their key characteristics and advantages.
TIG WELDING : THE PRECISION WELDING TECHNIQUE
TIG welding is a precise technique that yields strong and high quality welds. Microscopic TIG welding is used for welding tiny and intricate medical devices that require strength. It is also known as Gas Tungsten Arc Welding (GTAW). The following subtopics explains its essential characteristics and contributions:
- Unparalleled Precision – TIG welding excels in precision, enabling the fabrication of complex components and delicate medical instruments with slight deformation. Its controlled heat input and focused arc allow for the creation of precise welds, crucial for ensuring the functionality and durability of medical equipment.
- Clean and High Quality Welds – Clean and High-Quality Welds: TIG welding produces impeccable and high-quality welds, characterized by minimal spatter and extremely low risk of contamination. This is particularly important in medical equipment manufacturing, where sterility and hygiene are of supreme importance.
- Versatility and Compatibility- TIG welding adapts well to a variety of materials commonly used in medical equipment manufacturing, such as stainless steel, titanium, and non-ferrous metals. Its flexibility allows for the joining of various components, including tubes, sheets, and complex parts, thereby providing flexibility in the design and compilation of medical devices.
MIG WELDING: EFFICIENCY AND SPEED
MIG welding, also known as Gas Metal Arc Welding (GMAW), is another welding technique used in the production of medical equipment. It is a welding process that uses a consumable wire electrode and a shielding gas to join both pieces of a metal together. MIG welding is used in the manufacturing of medical equipment and devices like surgical tools, hospital beds, and diagnostic equipment.
The following subtopics shows the key benefits of MIG welding in this industry:
- High Productivity – MIG welding excels in high-speed and high-volume production, making it suitable for medical equipment manufacturing, where efficiency is of utmost importance. Its semi-automated or fully automated process allows for rapid weld deposition, minimizing production time and heightened output.
- Strong and Durable Welds – MIG welding yields strong and long lasting welds, providing exceptional joint integrity for vital medical equipment. This technique ensures solid weld penetration and better fusion, resulting in trustworthy and durable connections.
- Versatility in Material Compatibility – MIG welding demonstrates remarkable versatility when it comes to welding various materials used in the production of medical equipment, including stainless steel, aluminium, and mild steel. It makes room for a wide range of thicknesses, allowing the fabrication of diverse components for medical devices with ease and precision.
Ensuring Quality and Compliance
Both TIG and MIG welding play a pivotal role in establishing the quality and compliance of medical equipment manufacturing. The following subtopics describes their contributions in this regard:
- Precise Weld Inspection – The precise and regulated nature of TIG and MIG welding enables thorough scrutiny of welds, ensuring they meet the rigorous quality requirements of the medical industry. Non-destructive testing methods, such as visual inspection, radiography, and ultrasonic testing, are used to detect any distortions or imperfections.
- Compliance with Regulatory Standards – Medical equipment manufacturers must follow rigorous regulatory standards, such as ISO 13485 and FDA guidelines. TIG and MIG welding, with their ability to produce high-quality and trustworthy welds, highly contribute to meeting these regulatory mandates, ensuring the safety and effectiveness of medical devices.
Conclusion
TIG and MIG welding techniques play a vital role in the manufacturing of medical equipment where precision, quality and safety are of supreme importance. Their unmatched precision enables the fabrication of complex parts with minimal deformation, ensuring functionality and durability. The clean and extremely high-quality welds produced by these methods meet the strict requirements of the medical industry. Moreover, the flexibility of TIG and MIG welding allows for joining various materials and components, offering flexible designs. By maintaining regulatory standards and scrutinizing, these welding techniques contribute greatly to the safety, effectiveness, and compliance of medical devices. TIG and MIG welding truly stand as strong pillars in the creation of top-quality medical equipment.