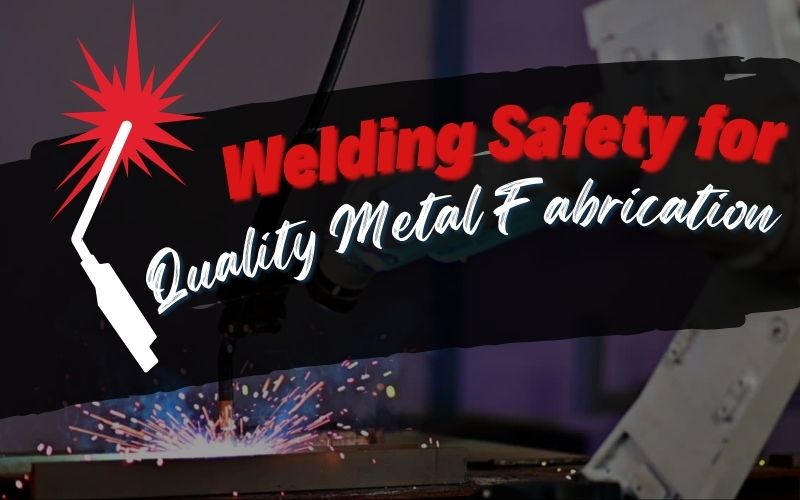
Welding Safety for Quality Metal Fabrication
“Safety isn’t just a slogan; it’s a vital component of every welder’s toolkit, ensuring quality fabrication without compromising well-being.”
Welding is an integral part of metal fabrication, playing a vital role in constructing structures and producing various metal products. Light welding fabrication, like any other welding work, carries inherent safety risks. However, through a proactive approach to safety, these hazards can be effectively alleviated. Recognizing the importance of working safely is as crucial as developing the skills required to excel in welding fabrication.
This article will highlight key safety measures that must be followed to achieve quality metal fabrication through safe welding practices.
Are you aware of the potential risks associated with welding?
- One of the most immediate threats is burns from the intense heat generated during the process.
- Additionally, welders are at risk of inhaling toxic fumes and gases emitted by the molten metal, which can lead to respiratory issues and long-term health problems.
- Furthermore, the electrical currents used in welding pose a risk of electric shock if proper insulation and grounding measures are not in place.
- Moreover, the high-intensity light produced during welding can cause eye injuries, including arc flash and retina burns, if workers do not wear appropriate protective gear.
Safety Measures
- Personal Protective Equipment (PPE) – The first line of defense against welding hazards is the use of appropriate personal protective equipment (PPE). Welders must wear flame-resistant clothing, including welding jackets, pants, gloves, and aprons, to safeguard against sparks, molten metal, and UV radiation. Additionally, a welding helmet equipped with a proper auto-darkening filter (ADF) is necessary to cover the eyes and face from harmful arc rays. Safety glasses with side shields, ear protection, and steel-toed boots should also be worn to provide total protection.
- Adequate Ventilation – It generates hazardous fumes and gases, including metal oxides, ozone, and nitrogen dioxide. These substances can be harmful if inhaled in excessive amounts. To ensure a safe working environment, proper ventilation must be practised in these areas. This can be achieved through natural or mechanical ventilation systems, such as local exhaust ventilation or fume extraction systems, which efficiently remove welding fumes from the breathing zone of the welder.
- Fire Prevention and Protection – It poses a significant fire hazard due to the presence of flammable materials and sparks. It is crucial to maintain a fire-safe workplace by removing combustible materials from the concerned area and implementing fire prevention measures. Adequate fire extinguishing equipment, such as fire blankets and extinguishers, should be readily available. Conducting regular fire drills and ensuring all workers are trained in fire safety protocols further enhance preparedness and reduce the risk of accidents.
- Electrical Safety – It involves high electrical currents, which can be dangerous if mishandled. Electrical shocks, burns, and fires are potential risks associated with welding equipment. To mitigate these hazards, welders should inspect cables, connectors, and grounding systems regularly for any signs of wear or damage. Grounding the workpiece and welding equipment is important to prevent electric shocks and ensure electrical stability during the welding process. Only skilled persons should handle electrical connections and repairs.
- Training and Certification – Employers must provide complete training programs that cover safe welding practices, hazard identification, and emergency procedures. Welders should be well-versed in the operation of welding machinery, use of PPE, and knowledge of the specific hazards associated with various welding processes. Certification programs, such as those offered by reputable organizations, validate a welder’s competency and understanding of safe working practices.
- Risk Assessment and Hazard Control – Conducting thorough risk assessments before commencing welding operations is essential. Identifying potential hazards and implementing appropriate control measures significantly minimize the risk of accidents. Hazard control measures may include implementing safety barriers, establishing restricted areas, and ensuring proper equipment maintenance. Regular inspections of equipment and machinery should be carried out to identify any defects that could compromise safety.
- Ergonomics and Workstation Design – Creating an ergonomic work environment is needed to lessen the risk of physical strain and injuries. Employers should design workstations that promote proper body positioning, reduce repetitive motions, and allow for comfortable and safe welding operations. Providing adjustable tables, ergonomic torches, and anti-fatigue mats can contribute to the overall well-being and productivity of welders.
These safety measures are a fundamental prerequisite for quality metal fabrication. By implementing comprehensive safety measures the employers uphold their commitment to both safety and quality, laying the foundation for a sustainable and successful metal fabrication industry.