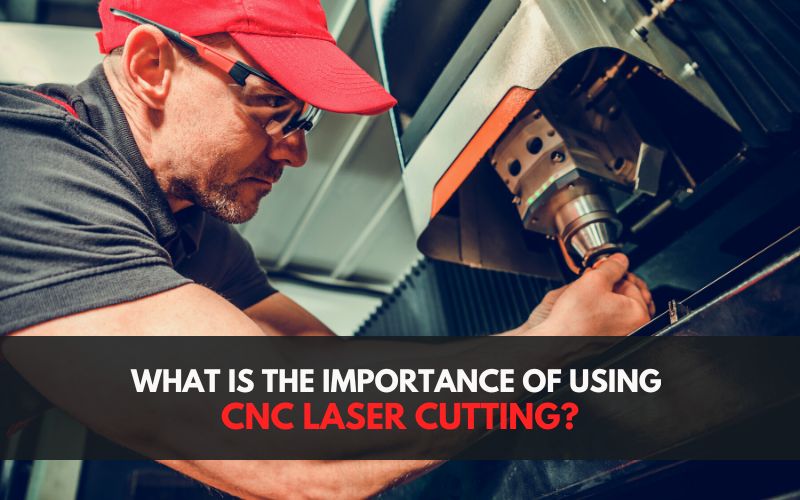
What Is the Importance of Using CNC Laser Cutting?
CNC laser cutting is a manufacturing process that uses a computer numerical control machinery to precisely cut, mark or engrave materials to create customized shapes. The CNC machine is equipped with a laser cutting system where the laser beam is directed onto the material to create unique designs. It is an efficient method used in various industrial sectors such as medical devices, automotive, jewellery, ceramic manufacturing, silicon , packaging, metalworks and so on….It is used in shaping materials such as metal, plastic, wood and more.
The importance of laser cutting lies in its highly accurate and steady method of cutting sheet metal and serves as an alternative to the etching process.
In this article we will discuss the importance of using the CNC laser cutting process.
- Higher Level of Precision – CNC laser cutting provides a high level of precision by delivering a focused beam of light. It also proves a higher accuracy level in cutting complicated designs and complex shapes. The laser beam is controlled by a computer, ensuring minimal wastage of material .
- Versatility – This method is flexible enough to be compatible with a wide range of materials, including metals, plastics, wood, glass, fabrics etc. It can cut materials of different thicknesses and densities, making it an adaptable tool for various industries.
- Cost Effectiveness – The CNC laser cutting is done with a single tool that is the laser beam.This eliminates the need for multiple tooling setups and reduces tooling costs which is not possible with the traditional cutting methods. There is no wear out of the surface hence maintenance cost is very less. GThe cost of operating the machine is also less than the traditional ones.
- Minimal Material Distortion – CNC laser cutting produces a narrow, focused laser beam that reduces heat transfer to the surrounding material. So the risk of distortion, warping, or damage to the material being cut is highly prevented which finally results in cleaner and more specific cuts.
- Speed and Efficiency – The speed at which the laser cuts through sheets takes lesser time. As a result, manufacturers can effortlessly prevent warping and distortion, saving valuable time in the process.
- Flexibility and Complex Designs – For each separate cut no extra tools are required in laser cutting. It allows you to create complicated designs with ease. Cuts with sharp corners and holes and complex patterns can be produced through CNC laser cutting. A lot of different shapes can be cut within the same material thickness.
- Real Time Monitoring & Error Detection – Advanced monitoring systems which are inbuilt in CNC laser cutting machines can detect anomalies like any irregularity in materials or cutting errors.These systems can automatically stop or alert the operators during any such issue in cutting process reducing any sort of flaws in the finished product.
- Reduced Tooling Cost – CNC laser cutting uses only a laser beam to cut through the materials which is very unlikely for traditional methods that use separate tools for cutting different materials. This eliminates the requirement for multiple tooling , thus reducing tooling setup costs.
- Safer Operation – CNC laser cutting systems are mapped with safety features to safeguard operators. The enclosed cutting area and automated operation reduces the risk of accidents and injuries associated with traditional cutting methods.
- Automation – This type of cutting process is highly automated using computer softwares. The cutting operation takes place automatically when all the design specifications are put into the machine. Need for manual labour is less in comparison with other cutting methods. Chances of errors caused due to human intervention or miscalculations are also less in number.
- Design and CAD/CAM Integration – CNC laser cutting systems are often integrated with Computer-Aided Design (CAD) and Computer-Aided Manufacturing (CAM) software.They ensure appropriate replication of the shapes and dimensions. This integration eliminates the need for manual measurements and transfers, thereby mitigating the potential for human error.
Conclusion
To sum up, CNC laser cutting plays an important role in modern manufacturing processes due to its various advantages. With high precision, consistency,speed and automated operation, CNC laser cutting diminishes human error, leading to higher accuracy and quality in cutting parts or components. The integration of CAD/CAM software further increases the efficiency by eliminating manual measurements reducing the risk of faults, thus creating a flawless product. This technology enables reliable replication of intricate shapes and dimensions, facilitating complex designs and boosting up production processes. By combining advanced technology, CNC laser cutting has become an indispensable tool, transforming several industries and delivering exceptional results in a wide range of applications.