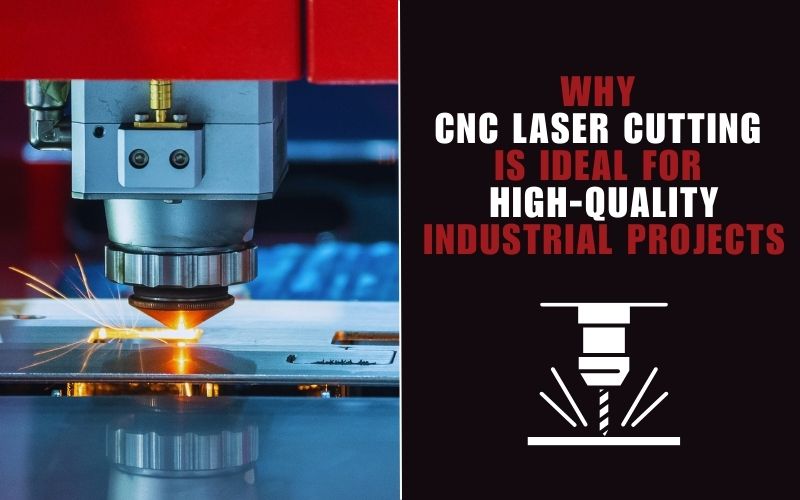
Why CNC Laser Cutting Is Ideal for High-Quality Industrial Projects
“Need Precision and Speed? CNC Laser Cutting Delivers Both!”
Accuracy and efficiency are crucial in industrial manufacturing. Businesses require cutting techniques that provide precision, quickness, and affordability. CNC laser cutting is an ideal choice. It guarantees top-quality outcomes for many industrial uses. Here’s why it is exceptional for industrial projects.
- Extreme Precision for Complex Designs
It offers numerous advantages in modern industry, starting with its higher level of precision minimizing the need for corrections. It uses lasers controlled by computers to provide high accuracy. The laser beam cuts according to precise instructions, allowing for complex designs. Whether you want detailed patterns, clean edges, or smooth surfaces, CNC lasers produce excellent results.This level of precision is important for fields such as aerospace, automotive, and electronics.
- Faster Production Speeds
Time is valuable in industrial projects. CNC laser cutting works quickly, which cuts down production time. Unlike older cutting methods, it doesn’t need tool changes. The laser moves smoothly, slicing through materials in just seconds.Fast cutting leads to quicker project finishes. Companies can stick to tight schedules without losing quality. This makes it ideal for large manufacturing tasks.
- Minimal Material Waste
This method of cutting generates minimal waste, making it an eco- friendly option. The precision of the laser beam ensures that cuts are clean and accurate, leaving little excess material. This efficiency not only conserves resources but also minimizes costs associated with material waste. Companies can optimize their budgets while promoting sustainability.
4. Versatility
It excels not only in metal but also in processing materials like wood, acrylic, and plastics. This versatility allows manufacturers to diversify their product offerings across various industries, including automotive, aerospace, and signage. Its broad application makes it a valuable asset for the metalworking industry and beyond, enhancing creativity and efficiency in production.
- No Physical Contact, No Damage
It uses a laser beam to cut materials without making contact. This method avoids friction, which means less wear and tear on tools. Since there is no mechanical pressure, the risk of distorting the material is lower. This helps keep delicate materials safe and results in high-quality products.
- Cost-Effective for Large-Scale Production
It lowers costs in several ways:
- Reduced waste: Optimized cutting patterns conserve materials.
- Minimized errors: Precision cutting eliminates the need for rework.
- Accelerated production: Shorter lead times decrease labor costs.
For high-volume manufacturing, these advantages lead to substantial savings. Businesses can produce high-quality parts more affordably, enhancing overall profitability.
- Consistency
It produces consistent results with every use, making it best suited for production runs that require consistency and uniformity.
- Easy Integration
These systems can easily integrate into existing production lines. This seamless transition reduces downtime and allows manufacturers to enhance their capabilities without major disruptions. The technology can complement other manufacturing processes, creating a more efficient workflow.
- Cleaner and Safer Work Environment
This is a safer option compared to traditional industrial cutting methods. It creates less debris, sparks, and dust, which helps keep the workspace tidy.Automated systems also mean fewer people are needed, which decreases the chance of accidents. With good ventilation and safety practices, it truly provides a safer place to work.
- Customization Opportunities
In today’s market, customization is key. It allows for easy modifications to designs. Manufacturers can quickly adapt to changing customer demands, producing unique products tailored to specific needs. This flexibility is essential in maintaining a competitive edge.
Moreover ,
- High Repeatability: It ensures consistent results with no damage to the material’s surface.
- Easy Programming: It can be programmed to process any design, making it cost-effective for cutting large metal sheets without molds.
- Adaptability: The process exerts no cutting force and generates no tool wear, allowing it to cut a wide range of materials.
All these features make CNC laser cutting the best choice for high-quality industrial projects.
Wrapping Up
As industries continue to evolve, embracing advanced technologies like CNC laser cutting will be definitely crucial. Companies looking to enhance their production capabilities should consider this innovative solution. By doing so, they can ensure they remain competitive in an ever-changing market.
Searching for the best solution provider for your Project?
Choose Mobifab: A Top Provider of Laser Solutions.
Our legacy of surpassing expectations includes a Mitsubishi SR-F laser cutter for speed and precision. Choose us for a flexible design approach, a dedicated team, and cutting-edge tools.