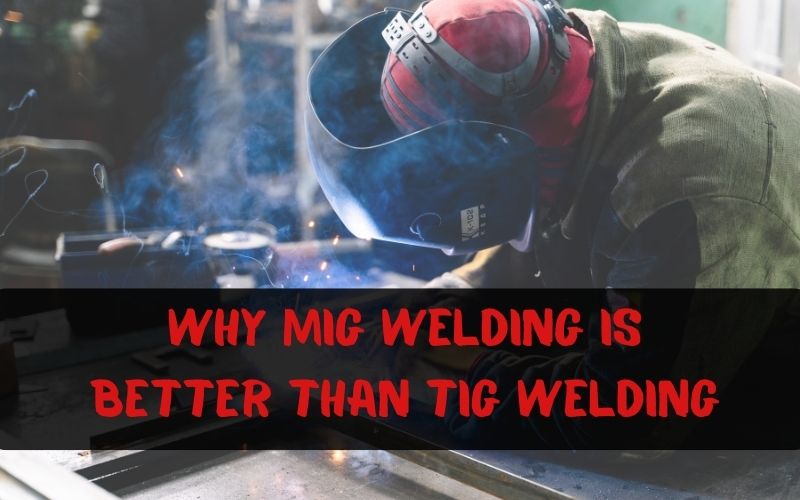
Why MIG Welding is Superior to TIG Welding
People often debate the question of whether MIG welding or TIG welding is better. After all, it’s natural to assume that different processes would result in different levels of quality. However, there are actually several ways in which MIG welding far outshines TIG welding in terms of quality and ease of use.
Let’s go over some of those ways now so that you can decide for yourself whether MIG welding or TIG welding should be the choice for you and your business!
What is MIG Welding?
MIG welding, or Metal Inert Gas welding, is a process for joining metals. When you use this type of welding, a gas-shielded electric arc heats up the metal and melts it. The molten metal from both surfaces then flows together and cools down to form the weld joint. The gas protects the weld from oxygen while it cools down, which creates a better bond than with other types of welding.
MIG welding can be done with any type of metal and it’s good for complex shapes because it doesn’t require much post-weld clean-up. It can also be used on pieces that are too thick or too thin for other types of welding because the heat isn’t concentrated in one area like with other types of welding methods.
What is TIG welding?
TIG welding, or tungsten inert gas welding, is a method of welding metals with a non-consumable electrode. The electrode uses an electric arc that heats up the metal enough to melt and bond them together.
The metal can be shaped by manipulating the arc’s location with a gasless filler metal. TIG welders are often used for thin sheet metal because it produces minimal spatter and offers precise control over molten pool location.
- MIG welding is faster than TIG welding
MIG welding is a type of welding that uses a wire feeder with an inert gas shielding. It can be used on steel, aluminium and stainless steel, and has been popular for some time in the automotive industry.
MIG welding has faster travel speeds than TIG welding because it does not require as much manual feeding of the filler metal. The filler metal is melted by an electric arc from the tungsten electrode that is powered by electricity from a power supply.
The molten weld pool can be manipulated by tilting the gun and moving it along in various directions to produce a greater variety of welds than with any other technique.
- MIG welding is less expensive than TIG welding
A MIG welding system consists of a gas powered welder, shielding gas and wire feeder. These three things combined make for much quicker and cheaper welds than TIG welding which only needs a welder and an electrode.
The wire feeder allows you to stay in one spot while the wire feeds through the gun and out the other side. This means that you don’t need to move around as much which saves time, money, and hassle since it’s not necessary to purchase two different welders. Not only does MIG welding save money but it also provides a higher quality weld with less spatter. With less spatter there are fewer chances for defects on your finished product.
- MIG welding is less likely to cause defects in the weld
MIG welding uses a shielding gas which protects the weld from the atmosphere. This shielding gas is usually a mixture of argon and carbon dioxide. The shield gas helps protect the weld from oxygen in the air, which can cause pitting in the weld and make it brittle.
Since oxygen cannot get into the weld with this type of welding, there are less defects created in the final product.
A disadvantage of MIG welding is that it requires an external power source because it does not use electricity like TIG welding does. This means that you need to make sure that you have an outlet nearby where you can plug in your welder so that you can produce enough energy for this type of welding.
- Last but never the least, MIG welding produces cleaner welds than TIG welding
MIG welds are a very popular welding process because they provide a cleaner and more attractive weld than the TIG welding process. The quality of the weld is due in large part to the shielding gas that comes with the wire.
The shielding gas protects the molten metal from oxygen which would otherwise cause porosity in the finished product and discolor it. During MIG welding, this shielding gas reduces spatter and results in a cleaner looking weld that does not require grinding or post-weld cleaning.